Tobacco (leaf tobacco) | [German version] |
Table of contents |
General: | ||
![]() |
Product information | |
![]() |
Packaging | |
![]() |
Transport | |
![]() |
Container transport | |
![]() |
Cargo securing |

Product information
Product name
German | Tabak (Rohtabak) |
English | Leaf Tobacco |
French | Tabac en Feuilles |
Spanish | Tabaco en rama |
Scientific | Nicotiana tabacum |
CN/HS number * | 2401 10 ff. |
(* EU Combined Nomenclature/Harmonized System)
Product description
Leaf tobacco consists of the dried and fermented leaves of the tobacco plant of the nightshade (Solanaceae) family. Tobacco is cultivated over an area extending from the tropics and subtropics to temperate latitudes such as the Mediterranean.
The tobacco plant is an annual with 20 to 30 leaves which may grow to 60 cm in size depending on variety and environmental conditions.
The following two tobacco types are of economic significance:
![]() |
Nicotiana tabacum L. (also known as Virginia tobacco) |
![]() |
Nicotiana rustica L. (also known as wild tobacco) |
Nicotiana tabacum L. is the most frequently transported type and is divided into the following varieties:
![]() |
Oriental tobaccos |
![]() |
Asian tobaccos, such as Sumatra and Borneo tobacco |
![]() |
American tobaccos, such as Virginia tobacco, Maryland tobacco, Kentucky tobacco, Brazilian tobacco, Burley |
After the 2nd World War, the American Blend cigarette, which is a mixture of Virginia, Burley and Oriental, became internationally predominant.
The tobacco constituents form primarily in the leaves and are not distributed evenly over the entire plant but rather occur in different concentrations depending on the position of the leaf.
The nicotine content in the tobacco leaves varies between 0.05% (Virginia tobacco) through 3 – 4% („Burley“) to 7.5% („Machorka“, Russia) [9].
Curing and fermentation constitute the crucial tobacco ripening processes. Where curing is concerned, a distinction is drawn between natural curing (sun curing of Oriental tobaccos, highly weather-dependent) and artificial curing (generally used for Virginia tobacco).
In the case of fermentation, a distinction is drawn between natural and chamber fermentation. When a cargo is accepted, it is advisable to have an assessor check the fermentation status, as chamber-fermented tobaccos tend to postferment during warm times of year.
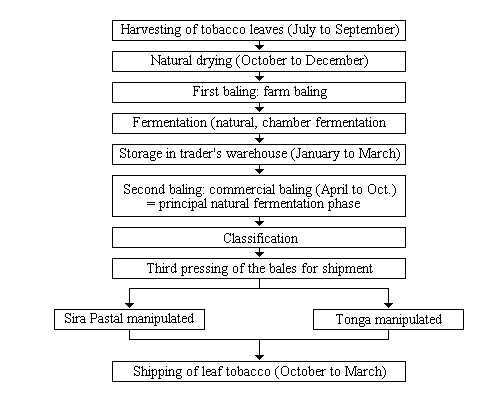
Figure 1: Processing flowchart for Oriental tobacco
Quality / Duration of storage
Ripening of the tobacco leaves starts towards the end of the vegetative period. During the ripening process, the chemical composition of the leaf changes, as do its color and elasticity.
The leaves are harvested when they have taken on a light green color. A distinction is drawn between:
![]() |
leaf harvest in 2 to 5 phases, at intervals from the bottom upwards (Virginia, Oriental, Burley) and |
![]() |
whole plant harvest, in which the topped plants are cut when an average degree of ripeness is reached (some Burley, Maryland, Machorka, cigar tobacco). |
The following different processing techniques are used, depending on the type and purpose of the tobacco:
Curing
naturally cured:
![]() |
air curing: Burley, Maryland, cigar tobacco etc. |
![]() |
sun curing: Oriental, some cigar tobacco |
![]() Figure 2 |
![]() Figure 3 |
artificially cured:
![]() |
hot air and flue curing: Virginia |
![]() |
fire curing: Kentucky, Latakia (Oriental) |
redrying
Virginia and some Burley and Maryland tobaccos are subjected to redrying after curing, for the purpose of sterilization, adjustment of moisture content and conditioning. During this procedure, the tobacco is dried at a high temperature (100°C) to a water content of 8 – 10% and, after cooling, then remoistened to a water content of 10 – 12%.
Fermentation
The fermentation process results in the formation of aromatic substances by means of enzymes and microorganisms and the breakdown of negative substances.
Aging
Aging is achieved by means of ferments, which have been blocked by the redrying process and slowly reactivate. The chemical changes to the main ingredients are slight, but the content of aromatic substances is markedly increased.
Processing techniques according to tobacco type:
Tobacco type | Harvesting method | Curing method | Pretreatment | Fermentation |
---|---|---|---|---|
Oriental tobaccos | leaf, phased | sun curing | – | bale fermentation or chamber fermentation |
Burley tobaccos | leaf, phased and whole plant | air curing | – | combined natural and chamber fermentation |
leaf, phased and whole plant | air curing | redrying | aging | |
Maryland tobaccos | leaf, phased and whole plant | air curing | redrying | aging |
Cigar tobaccos | leaf, phased and whole plant | air curing | stack fermentation | |
Virginia tobaccos | leaf, phased | flue curing | redrying | aging |
Kentucky tobaccos | whole plant | fire curing | redrying | strong fermentation |
whole plant | fire curing | redrying | aging |
At the time of harvest, a distinction is drawn between various leaf qualities depending on their height on the plant. These are harvested at different times (English names, from bottom to top, primings/flyings, lugs, cutters, leaf, tips).
![]() Figure 4 |
![]() Figure 5 |
![]() Figure 6 |
![]() Figure 7 |
The color of the leaf tobacco varies from golden yellow to dark brown, but does not determine quality.
Fine cigarette tobaccos consist of delicate, thin leaves with fine ribs (Oriental tobaccos). In lower quality varieties, the leaves are generally thicker and have strong, thick ribs.
Oriental tobaccos are particularly sensitive to high temperatures (> 25°C), as there is a risk of postfermentation. The risk increases especially in the warmer summer months.
Indicators of good and reduced-value tobacco bales:
Features | Good quality | Reduced-value product |
---|---|---|
Wrapping | clean and tight | dirty, torn, loose |
Distortion | – | distortion: warning sign of elevated intrinsic moisture content of the product |
Stains | – | brown water stains, dirt, dust, fats |
Mold | – | coating of white, gray, green or black mold |
Water content | 12 – 14% | water content < 12%: breakage of leaf mass on pressing. water content > 14%: bending of leaf mass on pressing. |
Temperature | < 25°C | measurement depends on localized temperatures; markedly increased temperatures are a warning sign of postfermentation. |
Intended use
Leaf tobacco is used for further processing, to produce the following end products: cigars, cigarettes, pipe tobacco, snuff, chewing tobacco.
Figures
(Click on the individual Figures to enlarge them.)
![]() Figure 8 |
![]() Figure 9 |
![]() Figure 10 |
![]() Figure 11 |
![]() Figure 12 |
![]() Figure 13 |
![]() Figure 14 |
![]() Figure 15 |
Countries of origin
This Table shows only a selection of the most important countries of origin and should not be thought of as exhaustive.
Europe | Turkey, Italy, Greece, France, Spain, Portugal, Bulgaria, Germany, Russia, Belgium, Croatia, Bosnia, Macedonia, Albania, Poland, Slovakia, Hungary, Ukraine, Moldova, Georgia, Azerbaijan, Uzbekistan, Kyrgyzstan |
Africa | Nigeria, Kenya, Uganda, Tanzania, Malawi, Zambia, Mozambique, Madagascar, Zimbabwe, South Africa, Cameroon, Ghana |
Asia | China, Indonesia, Japan, South Korea, India, Sri Lanka, Bangladesh, Thailand, Philippines, Pakistan, Burma, Iran |
America | USA, Canada, Brazil, Mexico, Dominican Republic, Guatemala, Colombia, Paraguay, Argentina |
Australia | Queensland, Victoria, New South Wales |
Back to beginning

Packaging
Virginia, Burley, Maryland, Kentucky and the like are packaged almost solely in cartons. The cartons are of internationally standard dimensions and weigh between 180 and 200 kg net. Since the leaf is deribbed where it is grown, leaf and ribs are packaged separately.
![]() Figure 16 |
Oriental tobacco and dark air-cured tobacco are generally packaged in jute bales, different weights being specific to different countries: Bulgaria approx. 22 kg net, Greece approx. 28 kg net, Turkey approx. 55 kg net, Malawi approx. 80 kg net, Indonesia approx. 100 kg net. Oriental tobaccos are generally Tonga manipulated, i.e. the tobacco leaves are compressed into bales in a random arrangement. Bales from Turkey, Greece and Albania are Sira-Pastal manipulated, i.e. the tobacco leaves are arranged in a single direction.
![]() Figure 17 |
The dimensions are approximately standardized. Some countries (e.g. China, India) also package lower quality Virginia tobaccos in bales.
Bales are generally wrapped in jute fabric. However, linen, palm leaves, banana leaves (Cuba), reed matting or bast are also used.
![]() Figure 18 |
![]() Figure 19 |
The growth in containerized transport has led to a decline in the use of hogsheads.
Back to beginning

Transport
Symbols
![]() General cargo |
Means of transport
Ship, truck, railroad. Ships are the main means of transport for tobacco; however, land transport by truck and railroad is also common.
Container transport
These days, tobacco is generally transported in 40′ or 20′ standard containers. Ventilated containers are only used for transport from regions with critical climatic conditions (e.g. Indonesia, Dominican Republic), subject to compliance with lower limits for water content of goods, packaging and flooring. Containers intended for loading have to be watertight and must not be contaminated in any way. Containers whose floors release a foreign odor, are contaminated by any substances or are too damp should be rejected. Below deck stowage is required, to rule out the possibility of exposure to rain or seawater or of overheating by day and cooling at night. Tobacco containers must not be stowed near heat sources.
Carton dimensions are adapted to container dimensions and allow the containers to be filled virtually to total capacity. These two features mean that the standard container can be used without difficulty as FCL cargo.
Cargo handling
Containers are often stuffed with cartons via locks (comparable to refrigeration locks), which provide protection against rain and snowfall. If the cartons are handled in the open air, the cargo must be protected from rain and snow and the like, since losses are otherwise inevitable.
When transporting leaf tobacco, the bales must be prevented from bumping against the hatch coaming, the ship’s sides, container walls or the like during packing, as the leaves of excessively dry tobacco may break under the slightest mechanical stress and thereby lose value. Hooks or cargo nets must not be used; instead, the tobacco must be loaded on pallets. Point loads must not occur at the corners and edges of the bales.
Stowage factor
![]() |
3.00 m3/t (Asian leaf tobacco from India, bales wrapped in jute fabric, 102 kg) [1] |
![]() |
5.70 m3/t (Oriental tobacco from Greece, bales wrapped in jute fabric, 29.2 kg) [1] |
![]() |
2.8 – 3.4 m3/t (American tobacco, corrugated board cartons, 200 kg) [14] |
![]() |
5.1 – 5.4 m3/t (American tobacco, bales from Havana, 50 kg) [14] |
![]() |
5.1 – 5.7 m3/t (American tobacco, bales from Brazil, 150 kg) [14] |
![]() |
4.0 – 4.8 m3/t (Asian tobacco, bales from China, 75 kg) [14] |
![]() |
2.3 – 3.4 m3/t (Asian tobacco, bales from Sumatra, 70 – 80 kg) [14] |
![]() |
2.8 m3/t (Asian tobacco, bales from Java, 80 kg) [14] |
![]() |
4.6 – 5.1 m3/t (Oriental tobacco, bales, 60 kg) [14] |
![]() |
3.1 – 3.6 m3/t (Oriental tobacco, small bales) [14] |
Stowage space requirements
Cool, dry, good ventilation. On board conventional ocean-going vessels, stowage spaces on the lower ‚tween deck are most favorable, as these do not adjoin any heat sources. Under no circumstances should tobacco bales be stowed beneath the metallic weather deck, as otherwise the risk of sweat formation is too great. The bales should stand on a completely flat, smooth surface. If the bales are stowed over boxes, distortion may arise, should the boxes shift as a result of rough seas. However, this negative effect may be ruled out by the use of appropriate dunnage.
Segregation
Fiber rope, thin fiber nets, matting, jute coverings. The segregation of individual batches is of considerable importance, as tobacco batches from different factories and of different varieties must not be mixed together.
Cargo securing
Since leaf tobacco suffers damage through breakage when exposed to the slightest mechanical stress, care must be taken to ensure that cargo securing is adequate, especially in the case of bales. The best course of action is to stuff the holds or containers completely full, so that the bales cannot move and bump into one another in the hold/container during transport.
Distortion caused by wooden dunnage is a particular risk with cigar wrapping leaves: if the leaves are torn, they can no longer be used as wrapping leaves.
Back to beginning

Risk factors and loss prevention
RF Temperature
Tobacco requires particular temperature, humidity/moisture and possibly ventilation conditions (SC VI) (storage climate conditions).
Designation | Temperature range | Source |
---|---|---|
Favorable travel temperature range | 20°C | [1] |
16 – 18°C | [4] | |
maximum 15°C | [57] | |
4 – 15°C | [14] |
If tobacco becomes heated because it has been stowed near heat sources or exposed to solar radiation, it dries out and the aromatic substances contained in it are volatilized. The tobacco then acquires a hay-like, bitter, sharp flavor. It may become hard and brittle, so meaning that the leaves break under the slightest mechanical stress and eventually end up as powder.
Oriental tobaccos are better transported during the cooler times of the year, as they are particularly sensitive to high temperatures (> 25°C) and there is a risk of postfermentation and of bale compression and thus of tobacco breakage.
Back to beginning

RF Humidity/Moisture
Tobacco requires particular temperature, humidity/moisture and possibly ventilation conditions (SC VI) (storage climate conditions).
Designation | Humidity/water content | Source |
Relative humidity | 65 – 70% | [1] |
50 – 60% | [4] | |
60 – 70% | [57] | |
Water content | 12 – 14% (Oriental tobacco) | [1] |
10 – 13% (Virginia tobacco) | [4] | |
10 – 12% (Virginia, Burley tobacco | [57] | |
12 – 14% (Oriental tobacco) | [57] | |
11 – 15% | [14] | |
Maximum equilibrium moisture content | 68% (Oriental tobacco) | [1] |
60 – 65% (Oriental tobacco) | [4] | |
50 – 65% (Virginia tobacco) | [4] | |
60 – 70% | [14] |
The main problems in transporting tobacco result from its hygroscopicity: conditioning of the tobaccos with respect to their water content (10 – 12% Virginia, Burley, 12 – 14% Oriental) is tightly specified. If the relative humidity is excessive, the tobacco absorbs so much water vapor that it becomes a nutrient medium for molds. Mold, mustiness, mildew stains and a musty odor reduce the quality of the tobacco. Oriental tobaccos are the most sensitive of all tobaccos to the effects of moisture. Their sorption isotherm shows that, at water contents of 12 – 14%, these tobaccos are at equilibrium with relative humidities of 60 – 65%. If the water content is higher than the recommended values (14%) or ventilation is inadequate (dead air zones), mustiness and decay may arise within just three days due to the mold Oespora tabaci. Depending on the type of mold, white, gray, green or black spots are visible in the tobacco bales.
![]() Figure 20 |
![]() Figure 21 |
Humidity, temperatures above 25°C and stack pressure promote postfermentation on extended storage.
Stack pressure causes the lowest layers of tobacco to deform, if excessively damp. The bales become compacted and completely worthless. Distortion may also arise in tobacco which has been improperly set down ashore (uneven ground).
Not only if storage conditions are excessively dry, but also if the optimum water content is exceeded, the tobacco loses aroma due to water vapor release. The tobacco then becomes less enjoyable, taking on a hay-like, bitter, sharp flavor. It may also become hard and brittle, so meaning that the leaves break under the slightest mechanical stress and eventually end up as powder.
Before the cargo is accepted, a certificate stating water content should be demanded from the consignor. If the tobacco is accepted at a later time (e.g. in the case of intermediate storage), the water content may have changed due to external influences and retesting is necessary.
Tobacco damaged by salt water or harbor water will be declared completely worthless by the receiver. Tobacco damaged by fresh water will give rise to objection only if moldy or musty. If moisture damage is suspected, testing is performed using the silver nitrate method, to find out whether chloride solutions (seawater) or fresh water (condensation or rain) are the cause.
Each drop of water which penetrates the wrapping of the tobacco bale colors the outside brown and the bales are deemed to be damaged.
Sufficient dunnage must be provided to ensure that the tobacco bales cannot come into contact with sweat water and metal components of the ship. Protection from sweat may be provided, for example, by covering the cargo with paper, gunny cloth or the like.
If tobacco bales are transported in containers, the latter must be absolutely watertight. Containers which are too damp should be rejected. Below deck stowage is required, to rule out the possibility of exposure to rain or seawater or of overheating by day and cooling at night and the resultant sweat formation. Tobacco containers must not be stowed near heat sources.
Back to beginning

RF Ventilation
Tobacco requires particular temperature, humidity/moisture and possibly ventilation conditions (SC VI) (storage climate conditions).
According to the cigarette manufacturer Reemtsma, conventional general cargo transport is becoming ever more unusual, having been largely replaced by container transport.
Tobacco is generally transported in 40′ or 20′ standard containers. Ventilated containers are only used for transport from regions with critical climatic conditions, such as Indonesia or the Dominican Republic.
If tobacco is loaded as conventional general cargo, ventilation is not normally required, provided that the water content of the tobacco corresponds to set values and there is no risk of sweat formation.
If this is not the case, [1] advises an air exchange rate of 6 changes/hour (airing) or just return air. Over-vigorous ventilation may dry out the tobacco and cause crumbling or fragmentation damage. For this reason, the system is switched to only vigorous return air.
Back to beginning

RF Biotic activity
Tobacco displays 3rd order biotic activity.
It belongs to the class of goods in which respiration processes are suspended, but in which biochemical, microbial and other decomposition processes still proceed, which, especially as a result of possible postfermentation, are associated with consumption of O2 and evolution of CO2.
Back to beginning

RF Gases
Due to continuing fermentation processes, an increased CO2 concentration and a consequent O2 shortage may occur in the hold. No access is permitted to the hold until it has been ventilated and the atmosphere tested with a gas detector.
Back to beginning

RF Self-heating / Spontaneous combustion
Under suitable conditions, tobacco has a tendency to postfermentation and self-heating. A slow rise in temperature of 0.5°C/d is of no significance; the tobacco is fully fermented. However, a rise in temperature of 2°C/d is a warning sign of incompletely fermented tobacco. For this reason, daily temperature measurements should be carried out when the cargo is conventionally loaded.
For example, if a rapid, abrupt rise in temperature to 50°C is observed, this is a warning sign of incompletely fermented tobacco which is undergoing postfermentation.
Back to beginning

RF Odor
Active behavior | Tobacco has a slight, pleasant odor and can taint other products with this typical odor. |
Passive behavior | Tobacco very readily absorbs foreign odors and thus must not be stowed together with, among others, the following products: drugs, spices, cosmetics, leather goods, kerosene, copra, ginger, camphor, hides, baled feathers, pulp, bitumen, resins, citrus fruits, essential oils, rubber and other odor-releasing products. |
Back to beginning

RF Contamination
Active behavior | Tobacco does not cause contamination. |
Passive behavior | Tobacco is extremely sensitive to contamination by dust, dirt, fats and oils. Contamination of the bales with liquids must be avoided. Workers in the port of loading must not rest containers of drinking water on the tobacco bales and, if they are chewing betelnuts, care must be taken to ensure that they do not spit on the bales because the betel colored saliva leaves indelible red stains. Tobacco bales are deemed to be damaged if even a slight red betel stain is visible. |
Back to beginning

RF Mechanical influences
Tobacco bales are extremely sensitive to mechanical stresses. When being loaded onto conventional cargo ships, the bales should be transferred on pallets. The use of hooks and cargo nets must be prohibited. Bumping, tumbling, uneven set-down surfaces and stack pressure result in distortion and compression. Broken and crushed tobacco leaves have reduced commercial value.
![]() Figure 22 |
Maximum stack heights:
Type | Stack height |
Oriental tobacco | 2.50 m (Greece, Black Sea) 3.60 m (Smyrna tobacco) |
Sumatra/Borneo tobacco (only wrapping leaves) | 7 bales high |
Brazilian tobacco (no wrapping leaves) | 7 – 9 bales high |
Back to beginning

RF Toxicity / Hazards to health
Due to continuing fermentation processes, an increased CO2 concentration and a consequent O2 shortage may occur in the hold. No access is permitted to the hold until it has been ventilated and the atmosphere tested with a gas detector.
Back to beginning

RF Shrinkage/Shortage
Excessively dry storage conditions may result in the water content falling below the admissible level due to release of water vapor. The tobacco loses its elasticity and fragmentation damage and evaporation losses occur.
Back to beginning

RF Insect infestation / Diseases
Tobacco pests include tobacco (or warehouse) moths, spider beetles, yellow mealworm beetles and bacon (or larder) beetles as well as the tobacco beetle. The tobacco beetle (Lasioderma serricorne), which is also known as the „cigarette beetle“, is in particular brought on board in the tropics and subtropics. It is 2 – 4 mm in length, brownish red to brownish yellow with gray hairs and a squat form. The larvae develop at temperatures of > 21°C and die at temperatures of as high as 10°C. The cocoons are attached to the interior of the packages (cartons, bales). Development from the egg to the imago (sexually mature adult stage) takes 2 months. Damage is primarily caused by the larvae eating the leaf, leaving behind circular holes 1 mm in diameter.
Tobacco is treated against tobacco pests prior to shipment in the warehouse or in the container. For the purpose of identifying any pests, traps are additionally set in the container which are checked on unpacking. Tobacco which has not been disinfected must not be stowed together with pest-free tobacco which has been disinfected in the country of production.
![]() Figure 23 |
Back to beginning

Additional information
The ocean-going vessel should be inspected and certified for fitness to carry tobacco. The shipper should also provide a certificate indicating the state of fermentation of the tobacco.
A distinction is drawn between old damage and transport damage:
Old damage may be identified by careful external inspection. Battered packaging, discoloration, water marks, uneven paperboard are typical types of damage which occur before loading.
Transport damage is primarily caused by leaks in the container, truck or railroad wagons. Incorrect setting down at the terminal (uneven ground) may also cause damage. In the event of moisture damage, testing is always performed using the silver nitrate method to determine whether the damage has been caused by seawater or rain water
Reference [4] lists the following types of damage in Oriental tobacco (tobacco bales) and their causes:
Type of damage | Causes |
---|---|
Sweat water, mold, rot | generally an excessively high water content |
Wet spots, mold, mustiness | poor ventilation of the hold/container |
Soaking and brown discoloration of the wrapping | fresh water |
Soaking, brown discoloration, plus white rings on the dried wrapping | salt water (but also possible due to salt content of the tobacco) |
Brown stains on the wrapping | dripping sweat water, spillage of drinking water at port of loading |
Distortion and compression | excessive stack height, excessive water content |
Torn, battered packaging | use of hooks, poor stowage |
Compression of lower layers of tobacco | incorrect laying of dunnage |
Slack bales and breakage of the leaf | desiccation, also due to cargo slippage |
Compression to form a solid mass | excessive stack height |
Fragmentation damage to tobaccos which had been stowed immediately below a metal weather deck | radiation weather |
Rust stains | inadequate protection from sweat dripping from rusty hold ceilings |
Dust damage | inadequate cleanliness of holds, dusty accompanying cargo |
Breakage | use of cargo nets or rope slings |
Back to beginning