Photo of the month – December 2024 |
[German version] |
![]() |
![]() |
Simply thoughtless or just not thought-through? |
Rolling Stones? |
Simply thoughtless or just not thought-through?
When production has finished, there necessarily comes the packaging. This has to protect the product, should cost as little as possible, has to be functional and must permit transportation, including the securing of the load. This, however, is an aspect that is almost universally ignored. Queries tend to result in answers such as “that’s the freight carrier’s responsibility, not ours” or something similar. That’s where the disaster lies, at the end of production when the thought process also often comes to a halt.
That is why the fiber drums that can be seen in the following photos are loaded in so desperate a way.
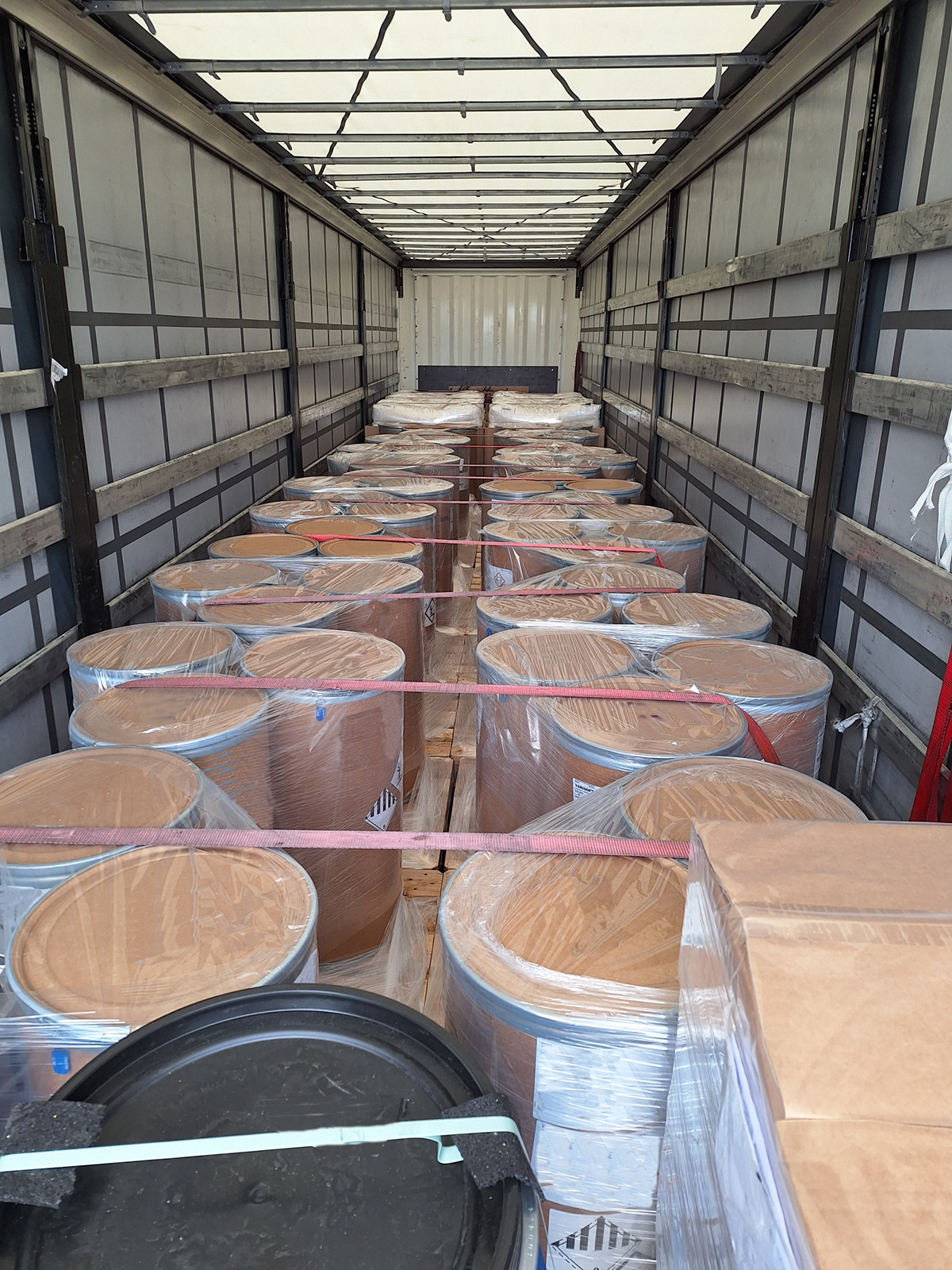
Figure 1 [Raymond Lausberg]
- Loading three fiber drums on each pallet must necessarily lead to gaps in the load
- There are gaps everywhere you look – the concept did not permit any form of tight fit
- Film wrappings applied half-heartedly at best
- Tie-down lashings that are presumably there just to look pretty, as they do absolutely nothing
- And all this when transporting dangerous goods.
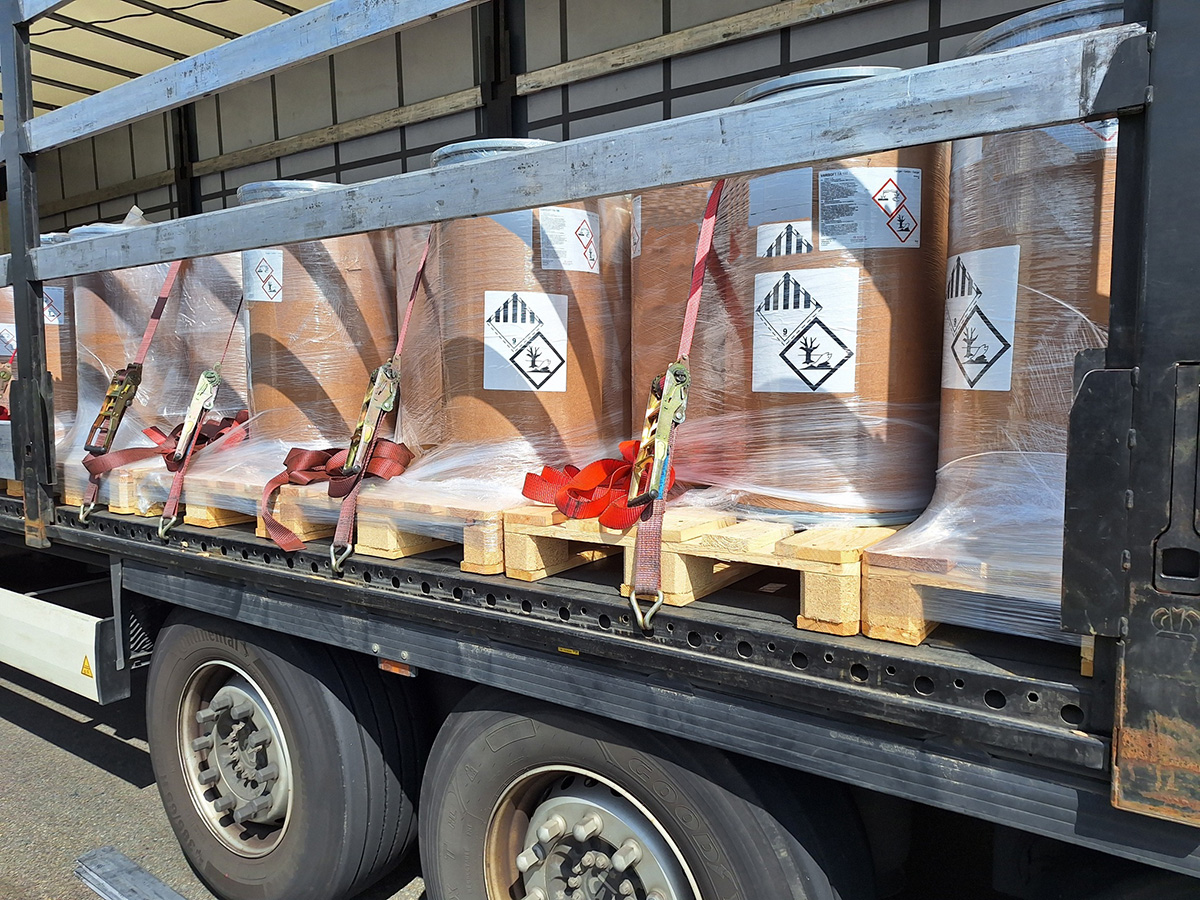
Figure 2 [Raymond Lausberg]
The only tight fit here was between the pallets. Even though they are fairly light at 54 kg per drum, the fiber drums were pretty much left to fend for themselves on the pallets. Sometimes there was a wrapping at the base to bind them to the pallets, sometimes not.
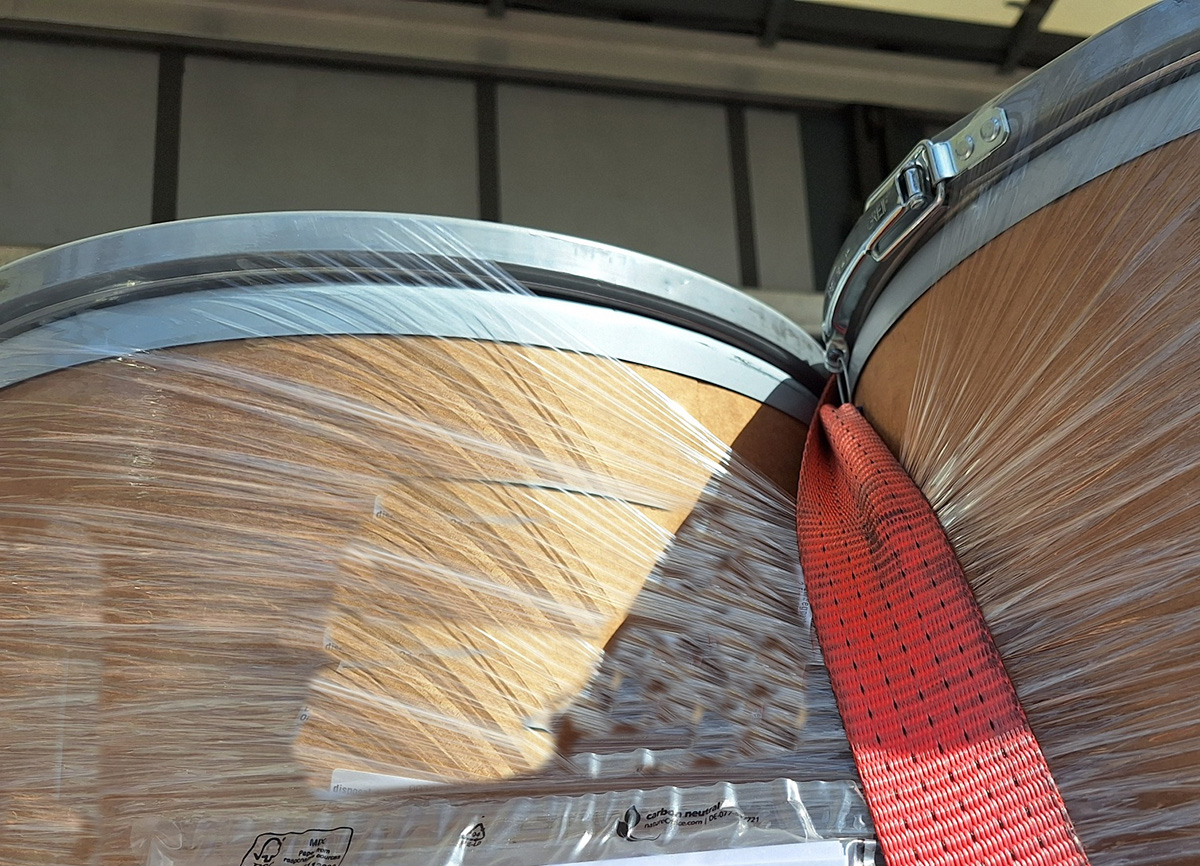
Figure 3 [Raymond Lausberg]
This photo says everything you need to know about the quality of the tie-down lashings. The video clip below shows exactly how well these belts were pretensioned…not at all. And there’s another thing that we would like to point out again here: When it comes to responsibility, the loader, carrier and driver act as one. The loader cannot escape this responsibility.
Video 1 [Raymond Lausberg]

Figure 4 [Raymond Lausberg]
The film wrapping matches everything else about this load. It has been applied or attached with very little pretensioning.
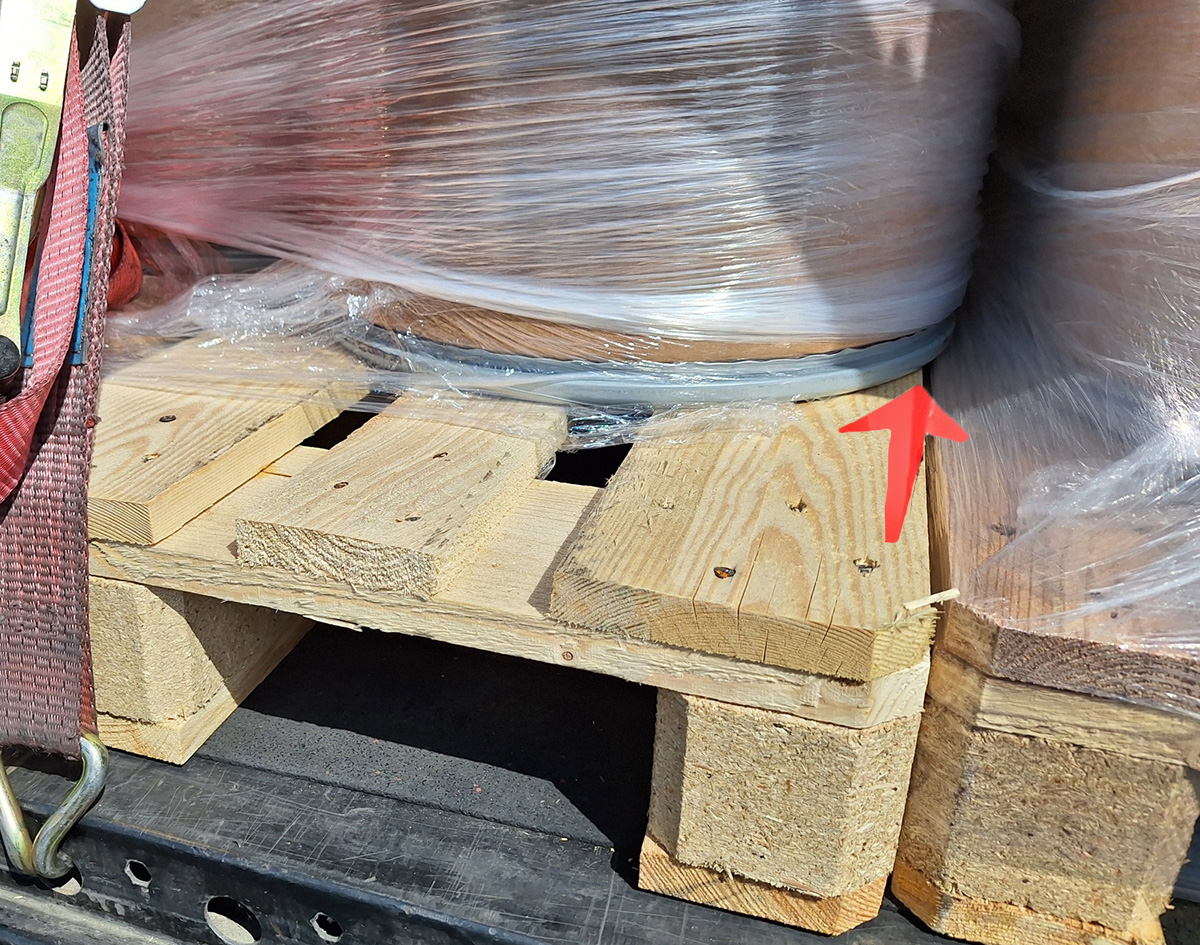
Figure 5 [Raymond Lausberg]
Here, there is no wrapping at all at the base, and when we look at the pallet on the right of the photo, we can see that the idea of binding the load to the pallet using the film really wasn’t taken very seriously. The left-hand fiber drum has already shifted forwards a little. After all, who or what was there to stop it?
Figure 6
One last example of the complete lack of thought that was at work here. These plastic barrels were held on the pallets by means of plastic straps. The anti-slip mats at the points where the straps pass over the covers were probably intended to prevent the barrels from sliding or to allow for a measure of elasticity. The video clip clearly shows that these straps were completely loose. Our eye is then caught by the red belt that was placed over the barrels like a tie-down lashing. If this had been even slightly pretensioned, the barrels would have tipped over and been able to slide against one another. The load securing effect is zero.
Securing the load:
- The fiber drums must be dimensioned in such a way that four of them can be grouped together on a pallet to form a load unit that has the best possible tight fit and that neither protrudes beyond the edge of the pallet nor ends short of it.
- When the film is applied, the pallet must be properly integrated into the wrapping in order to create a genuine load unit.
If the size is also chosen so that the load fits crosswise into the trailer (Code XL) in a way that produces a tight fit, then this tight fit in itself produces the load securing to the sides. - If there are still gaps in the load, then large hollow-section angle strips must be placed over the fiber drums in a way that makes effective tie-down lashing possible. It makes sense to use the strips to combine multiple load units into a single unit.
- Given the light weight of these fiber drums, the use of tie-down lashings also makes it possible to secure the load in the direction of travel.
- In the case of the blue plastic barrels, this is something of a challenge because the barrels themselves are flexible. If they are loaded to form a tight fit, they can bulge upwards and their flexibility means a lot of work is involved in securing them.
- One possibility is to use trays for these barrels. These are rigid, shaped plastic elements in which the barrels are placed like “coffee mugs”. To ensure that they are also secured at the top, a tray-like cover is used which also permits the load to be strapped securely. In this way, these flexible barrels can be grouped together to form rigid load units which can also be secured to the loading surface.
Your load securing columnists wish you a calm and peaceful Advent season.
Back to beginning