Classification of corrosion protection methods | [German version] |
![]() |
Active corrosion protection |
![]() |
Passive corrosion protection |
![]() |
Permanent corrosion protection |
![]() |
Temporary corrosion protection |

Active corrosion protection
The aim of active corrosion protection is to influence the reactions which proceed during corrosion, it being possible to control not only the package contents and the corrosive agent but also the reaction itself in such a manner that corrosion is avoided. Examples of such an approach are the development of corrosion-resistant alloys and the addition of inhibitors to the aggressive medium.
Back to beginning

Passive corrosion protection
In passive corrosion protection, damage is prevented by mechanically isolating the package contents from the aggressive corrosive agents, for example by using protective layers, films or other coatings. However, this type of corrosion protection changes neither the general ability of the package contents to corrode, nor the aggressiveness of the corrosive agent and this is why this approach is known as passive corrosion protection. If the protective layer, film etc. is destroyed at any point, corrosion may occur within a very short time.
Back to beginning

Permanent corrosion protection
The purpose of permanent corrosion protection methods is mainly to provide protection at the place of use. The stresses presented by climatic, biotic and chemical factors are relatively slight in this situation. Machines are located, for example, in factory sheds and are thus protected from extreme variations in temperature, which are frequently the cause of condensation. Examples of passive corrosion protection methods are:
![]() |
Tin plating |
![]() |
Galvanization |
![]() |
Coating |
![]() |
Enameling |
![]() |
Copper plating |
Back to beginning

Temporary corrosion protection
The stresses occurring during transport, handling and storage are much greater than those occurring at the place of use. Such stresses may be manifested, for example, as extreme variations in temperature, which result in a risk of condensation. Especially in maritime transport, the elevated salt content of the water and air in so-called seasalt aerosols may cause damage, as salts have a strongly corrosion-promoting action. The following are the main temporary corrosion protection methods:
![]() |
1. Protective coating method |
![]() |
2. Desiccant method |
![]() |
3. VCI method |
Back to beginning

1. Protective coating method
The protective coating method is a passive corrosion protection method. The protective coating isolates the metallic surfaces from the aggressive media, such as moisture, salts, acids etc..
The following corrosion protection agents are used:
![]() |
Solvent-based anticorrosion agents Very high quality protective films are obtained. Once the anticorrosion agent has been applied, the solvent must vaporize so that the necessary protective film is formed. Depending upon the nature of the solvent and film thickness, this drying process may take as long as several hours. The thicker the film, the longer the drying time. If the drying process is artificially accelerated, there may be problems with adhesion between the protective film and the metal surface. Since protective films are very thin and soft, attention must always be paid to the dropping point as there is a risk at elevated temperatures that the protective film will run off, especially from vertical surfaces. Since solvent-based corrosion protection agents are often highly flammable, they may only be used in closed systems for reasons of occupational safety. |
![]() |
Water-based anticorrosion agents Water-based anticorrosion agents contain no solvents and thus do not require closed systems. Drying times are shorter than for solvent-based anticorrosion agents. Due to their elevated water content, water-based anticorrosion agents are highly temperature-dependent (risk of freezing or increased viscosity). The advantage of this method is that the protective film is readily removed, but the elevated water content, which may increase relative humidity in packaging areas, is disadvantageous. |
![]() |
Corrosion-protective oils without solvent Corrosion-protective oils without solvent produce only poor quality protective films. Good quality protection is achieved by adding inhibitors. Since these corrosion-protective oils are frequently high quality lubricating oils, they are primarily used for providing corrosion protection in closed systems (engines etc.). |
![]() |
Dipping waxes The protective layer is applied by dipping the item to be packaged into hot wax. Depending upon the type of wax, the temperature may have to be in excess of 100°C. Removal of the protective film is relatively simple as no solid bond is formed between the wax and metal surface. Since application of dipping waxes is relatively complex, its use is limited to a few isolated applications. |
Back to beginning

2. Desiccant method
Introduction
According to DIN 55 473, the purpose of using desiccants is as follows: „desiccant bags are intended to protect the package contents from humidity during transport and storage in order to prevent corrosion, mold growth and the like.“
The desiccant bags contain desiccants which absorb water vapor, are insoluble in water and are chemically inert, such as silica gel, aluminum silicate, alumina, blue gel, bentonite, molecular sieves etc.. Due to the absorbency of the desiccants, humidity in the atmosphere of the package may be reduced, so eliminating the risk of corrosion. Since absorbency is finite, this method is only possible if the package contents are enclosed in a heat sealed barrier layer which is impermeable to water vapor. This is known as a climate-controlled or sealed package. If the barrier layer is not impermeable to water vapor, further water vapor may enter from outside such that the desiccant bags are relatively quickly saturated, without the relative humidity in the package being reduced.
Desiccants are commercially available in desiccant units. According to DIN 55 473:
„A desiccant unit is the quantity of desiccant which, at equilibrium with air at 23 ± 2°C, adsorbs the following quantities of water vapor:
![]() |
min. 3.0 g at 20% relative humidity |
![]() |
min. 6.0 g at 40% relative humidity |
The number of desiccant units is a measure of the adsorption capacity of the desiccant bag.“
Desiccants are supplied in bags of 1/6, 1/3, 1/2, 1, 2, 4, 8, 16, 32 or 80 units. They are available in low-dusting and dust-tight forms. The latter are used if the package contents have particular requirements in this respect.
Calculation of required number of desiccant units
The number of desiccant units required is determined by the volume of the package, the actual and desired relative humidity within the package, the water content of any hygroscopic packaging aids, the nature of the barrier film (water vapor permeability).
Formula for calculating the number of desiccant units in a package (DIN 55 474):
n = (1/a) × (V × b + m × c + A × e × WVP × t)
n | number of desiccant units | ||||
a | quantity of water absorbable per desiccant unit in accordance with the maximum admissible humidity in the package: | ||||
admissible final humidity | 20% | 40% | 50% | 60% | |
factor a | 3 | 6 | 7 | 8 | |
e | correction factor, relative to admissible final humidity in %: | ||||
admissible final humidity | 20% | 40% | 50% | 60% | |
factor e | 0.9 | 0.7 | 0.65 | 0.6 | |
V | internal volume of the package in m3 | ||||
b | absolute humidity of enclosed air in g/m3 | ||||
m | mass of hygroscopic packaging aids in kg | ||||
c | factor for the moisture content of hygroscopic packaging aids in g/kg | ||||
A | surface area of barrier film in m2 | ||||
WVP | water vapor permeability of barrier film under anticipated climatic conditions in g/m2d, measured to DIN 53 122, Pt. 1 or Pt. 2 (d = day) | ||||
t | total duration of transport in days |
The following sample calculation reveals the location of the greatest potential risks:
A German manufacturer is to export a packaging machine to a customer in Brazil. The machine is packaged in wooden box of the following dimensions:
Lengthinternal | : | 7.00 m | |
Widthinternal | : | 2.75 m | |
Heightinternal | : | 3.00 m |
This gives an internal volume (V) of: 7.00 m × 2.75 × 3.00 m = 57.75 m3.
The area (A) of the barrier layer is calculated on the basis of the area of the internal sides of the box:
2 × (7.00 m × 2.75 m) | = 38.50 m2 | |
2 × (7.00 m × 3.00 m) | = 42.00 m2 | |
2 × (2.75 m × 3.00 m) | = 16.50 m2 | |
Total | = 97.00 m2 |
The packaging machine is secured by bracing with 6 pieces of squared pinewood lumber. These are located inside the climate-controlled package. The lumber is air dry, its water content is 15% => factor for moisture content of hygroscopic packaging aid (c) = 150 g/kg.
The dimensions of the squared lumber are 2.70 m × 0.20 m × 0.20 m (L×W×H). At an approximate density of pinewood of 500 kg/m3, the mass (m) is as follows:
6 × 2.70 m × 0.20 m × 0.20 m = 0.648 m3 | |
0.648 m3 × 500 kg/m3 = 324 kg of lumber |
The following assumptions were also made:
Admissible final humidity was stated at 40%. (a) thus = 6 g and (e) = 0.7
An aluminum composite film is used as the barrier layer, the water vapor permeability (WVP) of which is 0.1 g/m2d.
The absolute humidity of the enclosed air (b) is 13.8 g/m3 at 20°C and 80% relative humidity
Corrosion protection should last for a total of 100 days (d).
When these values are inserted in the equation, the following result is obtained:
n = 1/6 g × [(57.75 m3 × 13.8 g/m3) + (324 kg × 150 g/kg) + (97 m2 × 0.7 × 0.1 g/m2d × 100 d)] |
n = 1/6 g × (796.95 g + 48600.00 g + 679.00 g) |
n = 1/6 g × 50075.95 g |
n = 8346 desiccant units |
The calculation demonstrates that a total quantity of 50075.95 g of water vapor is present inside the climate-controlled package or diffuses through the barrier layer. A total of 8346 desiccant units would have to be placed in the box to absorb this quantity of water vapor, which is not a practical proposition. Taking a closer look at the details of the calculation reveals the greatest potential risks:
V × b | = | 796.95 g | = | the water vapor present in the enclosed air |
m × c | = | 50075.95 g | = | the water vapor bound in the hygroscopic packaging aids |
A × e × WVP × t | = | 679.00 g | = | the water vapor which diffuses through the barrier layer over the entire period of protection |
It is clear from the above that the hygroscopic packaging aids in the climate-controlled package are responsible for the greatest potential risk, so it would be advisable to locate these outside the barrier layer. However, any screws, bolts or nails which pass through the barrier layer must then be appropriately sealed. The required quantity of desiccant would consequently change as follows.
n = 1/6 g × ( 796.95 g + 679.00 g ) | |
n = 246 desiccant units |
This number of desiccant units may easily be accommodated in the box in question.
When calculating the required number of desiccant units to DIN 55 474, care must be taken to assume that all the water present in the climate-controlled package must be absorbed by the desiccant. It is accordingly assumed that, as in the present example, the squared lumber will dry to a water content of 0%. In reality, however, this is not the case as at a relative humidity of 40% (agreed admissible final humidity), the water content of pinewood is still approx. 8% and this water is not released from the lumber. However, this fact is not taken into account in the calculation, which means that the calculated number of desiccant units is actually too high. On the basis of the above example, this would make the following difference:
![]() |
drying to a water content of 0%: 150 g/kg × 324 kg = 48600 g of water |
![]() |
drying to a water content of 8%: 80 g/kg × 324 kg = 25920 g of water |
48600 g – 25920 g = 22680 g of water are released on drying from 18% to 8%.
The required number of desiccant units may then be calculated as follows:
n = 1/6 g × (796.95 g + 22680.00 g + 679.00 g) | |
n = 1/6 g × 24155.95 g | |
n = 4026 desiccant units |
As a result, the number of desiccant units required would fall by 4320 units. The quantity of desiccant units is nevertheless still so large that they are virtually impossible to accommodate. The fact still remains that the hygroscopic packaging aids remain the greatest potential risk in the climate-controlled package.
Barrier films
Barrier films are available in various forms, for example as a polyethylene film or as a composite films with two outer polyethylene layers and an aluminum core. The composite film performs far better with regard to water vapor permeability (WVP), achieving WVP values of below 0.1 (g/m2d). In the composite film, the barrier layers are arranged so as to bring about a considerable reduction in permeability in comparison with a single layer.
In accordance with current DIN standards, water vapor permeability is always stated for both 20°C and 40°C. According to information from the manufacturer, it may be concluded that water vapor permeability rises with increasing temperature and falls with increasing thickness. This problem occurs most particularly with polyethylene films, while aluminum composite films are largely insensitive to rises in temperature.
Placement of desiccant bags
The desiccants should be suspended from strings in the upper part of the climate-controlled package to ensure good air circulation around them.
It is essential to avoid direct contact between the desiccant bag and the package contents as the moist desiccant would promote corrosion.
It is advisable to use numerous small bags rather than fewer large ones, as this increases the available surface area of the desiccant and so improves adsorption of the water.
In order to ensure the longest possible duration of protection, the barrier film must be heat sealed immediately once the desiccant bags have been inserted.
Desiccant bags are always supplied in certain basic package sizes which, depending upon the desiccant unit size, may contain a single bag (of 80 units) or up to 100 bags (of 1/6 unit). The basic outer package should only be opened directly before removal of a bag and must immediately be heat sealed again.
Comparison of advantages and disadvantages of the desiccant method
Advantages
![]() |
Desiccants provide excellent corrosion protection to both metallic and nonmetallic items |
![]() |
Removal of the desiccant on delivery to the receiver is straightforward, unlike the removal of protective films in the protective coating method. The package contents are immediately available. |
![]() |
No particular occupational hygiene requirements apply as the desiccant is nonhazardous. |
Disadvantages
![]() |
Placement of the desiccant bags and heat sealing of the barrier films are relatively labor-intensive. |
![]() |
The slightest damage to the barrier layer may negate the effectiveness of corrosion protection. |
![]() |
Calculating the required number of desiccant units is not entirely simple and it is easy to overcalculate. However, too much protection is better than too little. |
![]() |
Humidity indicators inside the package are not very reliable as they are only valid for certain temperature ranges. |
Back to beginning

3. VCI (Volatile Corrosion Inhibitor) method
Mode of action and use
Inhibitors are substances capable of inhibiting or suppressing chemical reactions. They may be considered the opposite to catalysts, which enable or accelerate certain reactions.
Unlike the protective coating method, the VCI method is an active corrosion protection method, as chemical corrosion processes are actively influenced by inhibitors.
In simple terms, the mode of action (see Figure 1) is as follows: due to its evaporation properties, the VCI substance (applied onto paper, cardboard, film or foam supports or in a powder, spray or oil formulation) passes relatively continuously into the gas phase and is deposited as a film onto the item to be protected (metal surfaces). This change of state proceeds largely independently of ordinary temperatures or humidity levels. Its attraction to metal surfaces is stronger than that of water molecules, resulting in the formation of a continuous protective layer between the metal surface and the surrounding atmosphere which means that the water vapor in the atmosphere is kept away from the metal surface, so preventing any corrosion. VCI molecules are, however, also capable of passing through pre-existing films of water on metal surfaces, so displacing water from the surface. The presence of the VCI inhibits the electrochemical processes which result in corrosion, suppressing either the anodic or cathodic half-reactions. Under certain circumstances, the period of action may extend to two years.
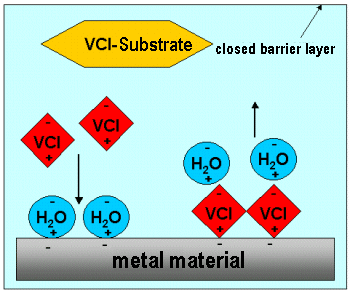
Figure 1: Mode of action of VCI
The mode of action dictates how VCI materials are used. At item to be protected is, for example, wrapped in VCI paper. The metallic surfaces of the item should be as clean as possible to ensure the effectiveness of the method. The VCI material should be no further than 30 cm away from the item to be protected. Approximately 40 g of active substances should be allowed per 1 m³ of air volume. It is advisable to secure this volume in such a manner that the gas is not continuously removed from the package due to air movement. This can be achieved by ensuring that the container is as well sealed as possible, but airtight heat sealing, as in the desiccant method, is not required.
The VCI method is primarily used for articles made from carbon steel, stainless steel, cast iron, galvanized steel, nickel, chromium, aluminium and copper. The protective action provided and compatibility issues must be checked with the manufacturer.
N.B.: The use of water-miscible, water-mixed and water-immiscible corrosion protection agents, corrosion protection greases and waxes, volatile corrosion inhibitors (VCI) and materials from which volatile corrosion inhibitors may be released (e.g. VCI paper, VCI films, VCI foam, VCI powder, VCI packaging, VCI oils) is governed by the German Technical Regulations for Hazardous Substances, TRGS 615 „Restrictions on the use of corrosion protection agents which may give rise to N-nitrosamines during use“.
Comparison of advantages and disadvantages of the VCI method
Advantages
![]() |
Since the gas also penetrates holes and cavities, these areas also receive adequate protection. |
![]() |
The period of action may extend to two years. |
![]() |
The wrapping need not be provided with an airtight heat seal. |
![]() |
On completion of transport, the packaged item need not be cleaned, but is immediately available. |
Disadvantages
![]() |
The VCI method is not suitable for all metals. It may cause considerable damage to nonmetallic articles (plastics etc.). |
![]() |
Most VCI active substances may present a hazard to health, so it is advisable to have their harmlessness confirmed by the manufacturer and to obtain instructions for use. |
Back to beginning