Photo of the month – January 2024 |
[German version] |
When fixed belts come loose…
A full load of wire rod coils weighing a total of 24,000 kg. What made this load different from many of its kind was the fact that all the coils were loaded in an orientation that allowed them to roll in the direction of travel (“rolling direction”). This is in itself not a fatal error and is certainly not uncommon. However, it does dramatically increase the required load securing work. Nevertheless, this can be dealt with very effectively using direct lashings.
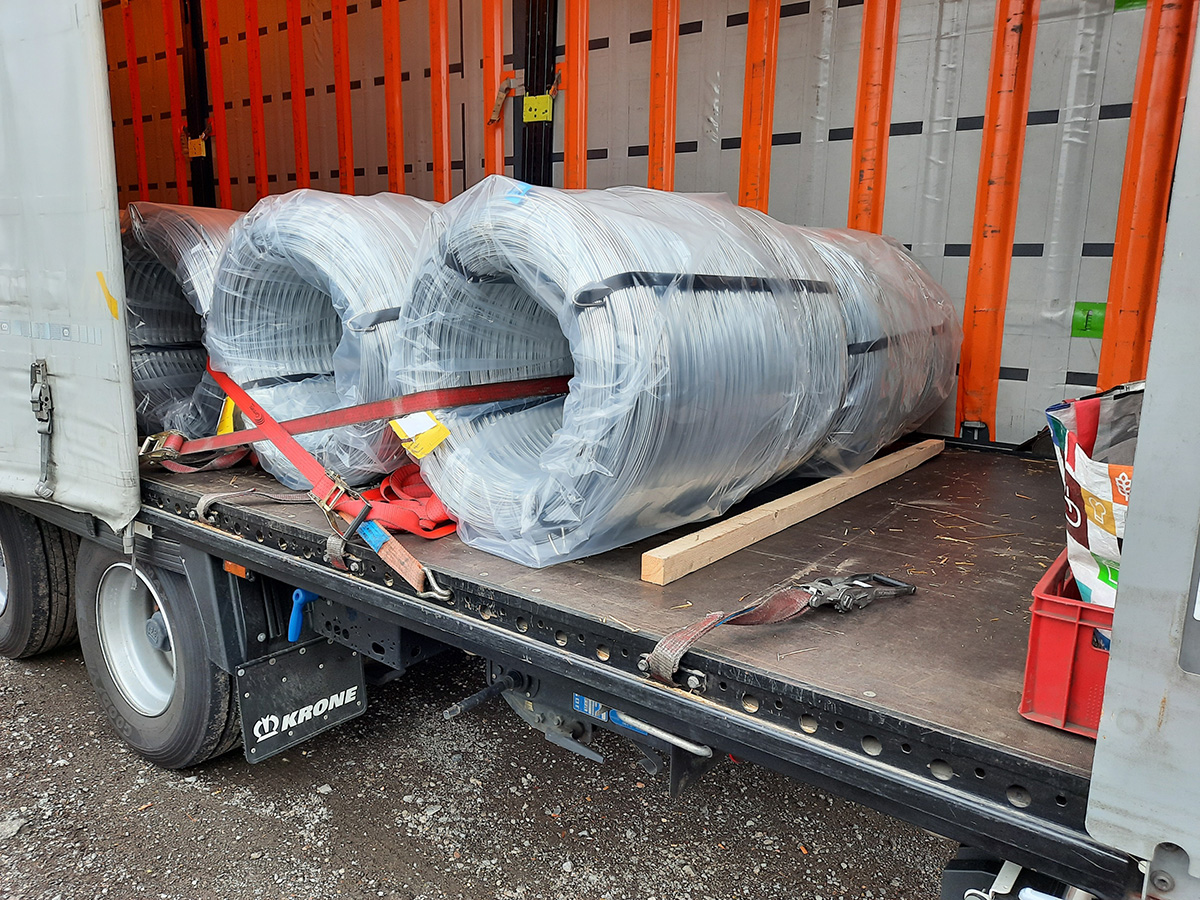
Figure 1 [Raymond Lausberg]
No sooner said than done! Here, the loaders not only used direct lashings but did so in both directions (to the front and the rear).
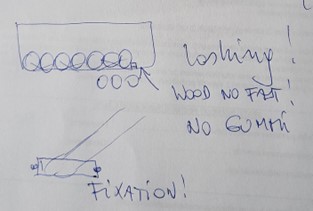
Note from the official who took the photographs [PotM]
Since we have no photograph showing the entire load, we refer here to part of a note made by the official who took the photos and kindly made his notes available to us.
The load was secured as follows:
Three loop lashings in each direction, adding up to 12,000 daN of securing force per direction. A small negative point can be noted with regard to the angles, although this is of little consequence given that very effective angles were chosen. Assuming that the end wall complied with Code XL requirements, then the load securing could very well be adequate, at least in the direction of travel.
We will therefore take a closer look at two more serious issues:
1.) Pretensioning
The pretensioning of the direct lashings was simply missing. This is unacceptable when direct lashings are used because the load is able to move up against loose belts and can travel a short distance, gaining kinetic energy as it does so. This movement is then suddenly arrested by the load securing equipment. It is not possible to calculate the forces released during this process because the load has, to all intents and purposes, been able to “take a run-up”. The belts must be pretensioned to ensure that any movement is guided into pretensioned load securing equipment without being propelled into it by a long run-up. Depending on the direction of acceleration, the tensioning on the opposite side is relaxed and the corresponding pretensioning made available as load securing force at the initiating side.
2.) Attachment of the belts
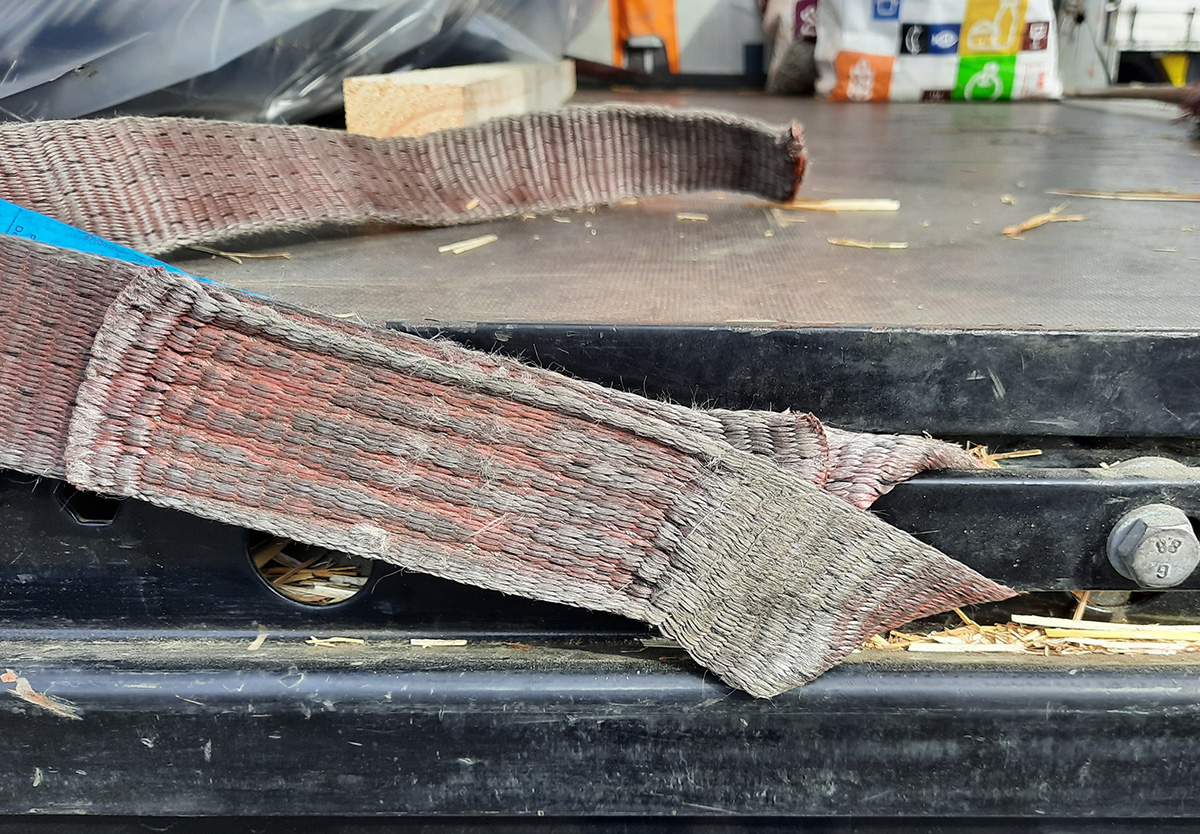
Figure 2 [Raymond Lausberg]
The real problem of this load and of the way it is secured lies in the “fixed belts”. We use the term “fixed belts” to describe belts which are firmly attached to the vehicle, for example using screw connections. These are often found on trailers, which are primarily used unaccompanied in combined (intermodal) transport. This is a good thing because it means that the belts cannot be separated from the trailer. HOWEVER, they can then only be used as tie-down lashings and not as direct lashings as in our example. Figure 3 impressively illustrates what happens to the belts when they are used almost horizontally. The belts become pinched, causing them to lose as much as 90% or more of their restraining force because, when subjected to a load, the warp yarns tear one by one due to the fact that the belts no longer bear the force across their full width but only at the outside edge.
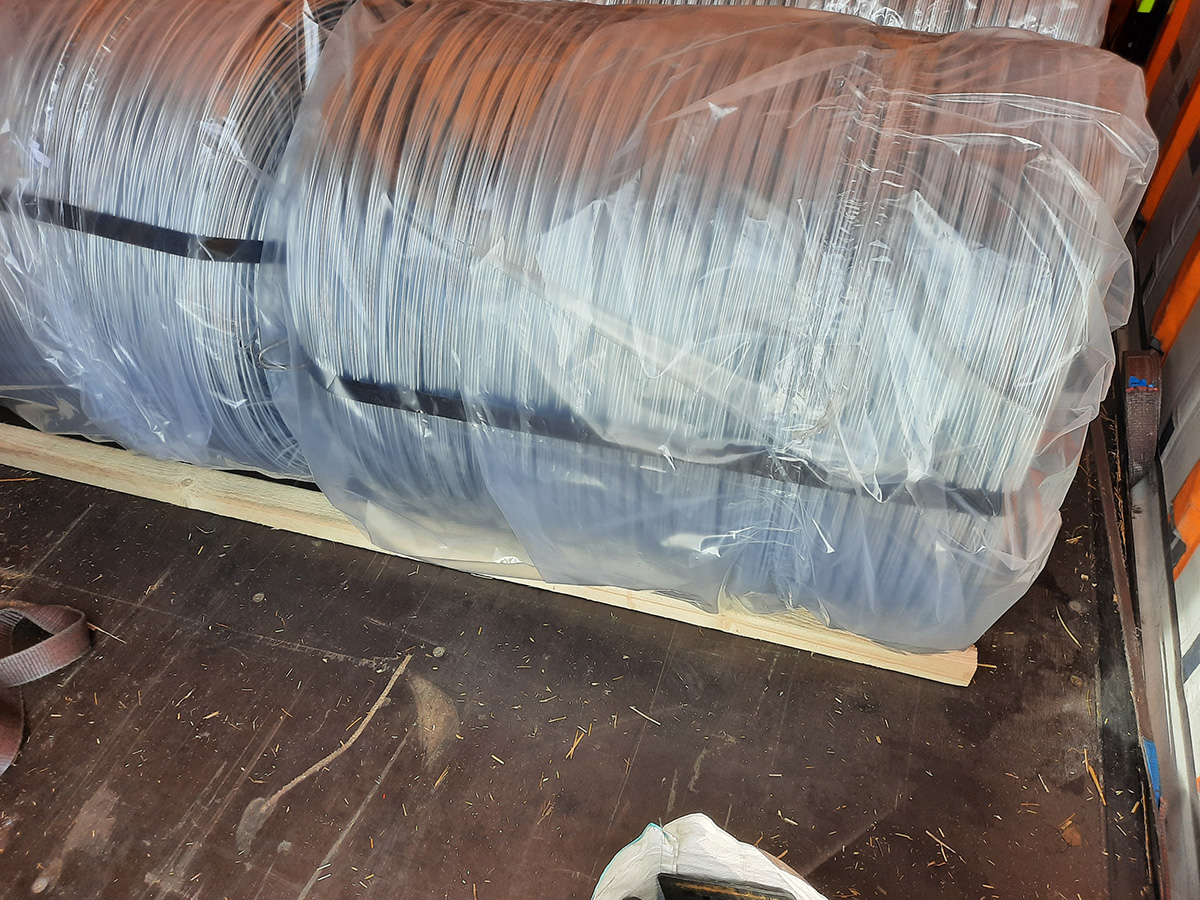
Figure 3 [Raymond Lausberg]
The squared lumber lying behind the load was not attached to anything and was only used for safety reasons during the loading operation to prevent the coils from rolling away before they were secured. This can be seen in the short video excerpt.
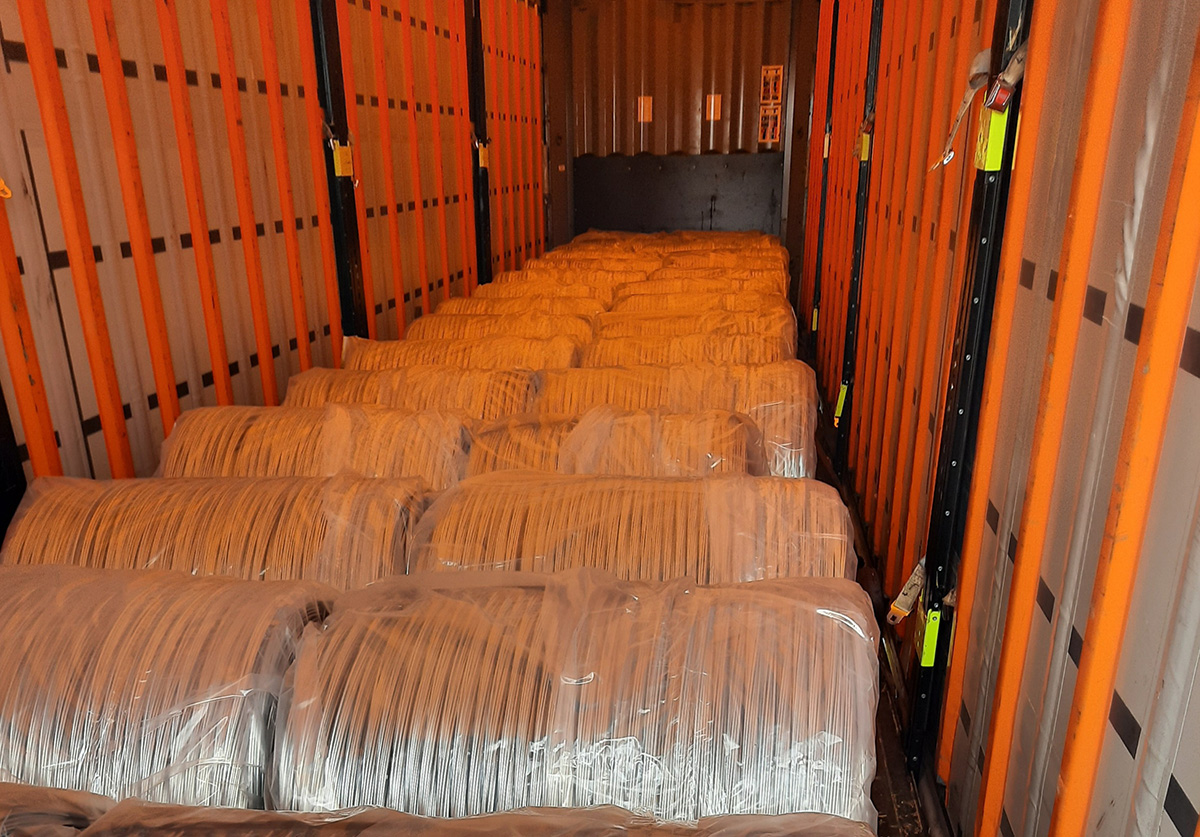
Figure 4 [Raymond Lausberg]
All in all, this looks like an excellent vehicle: The tarpaulin appears to be reinforced by slats in the vertical direction and this undoubtedly greatly enhances the securing measures when the cargo is loaded as a tight fit. Unfortunately, this load benefited neither from a tight fit nor from any securing to the side. The plastic sheeting may reduce the already poor level of friction even further. For safety’s sake, we assume a coefficient of friction of µ = 0.2. As a result, additional securing force of 7,200 daN must be provided to each side. Regular readers of our column will know that we would only ever use loop lashings to provide this kind of securing force. To do this, we always gather together six coils in a group by means of a direct lashing and then guide the belt back to the same side of the vehicle. Of course, this direct lashing must be undertaken on both sides of the vehicle.
Your load securing columnists wish you a safe and secure 2024
Back to beginning