Photo of the Month – May 2023 |
[German version] |
Blocks with handles or
how to secure ingots
Ingots are bars that usually take the form of long metal bodies which, presumably due to the methods used to cast them, have a conical shape. Ingots are frequently made from a pure, single metal. However, alloys are also cast in this way and transported to other locations for further processing.
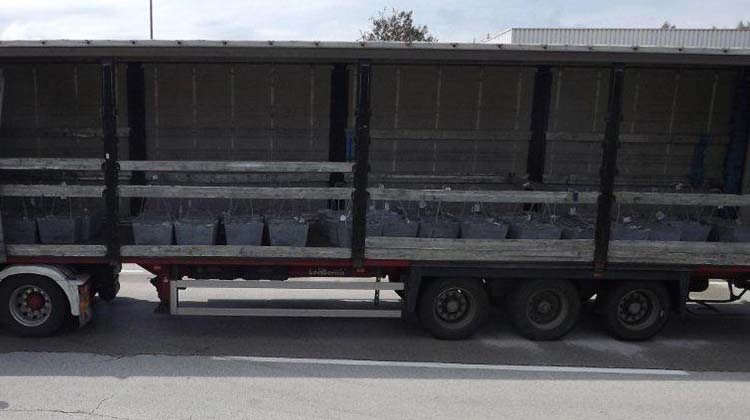
Figure 1 [Karl-Heinz Pachoinig]
Here we see a trailer fully loaded (24 tonnes) with ingots. They are restrained only by their friction. Due to their weight, it was probably thought that no other effort had to be made and this was naturally a terrible miscalculation!
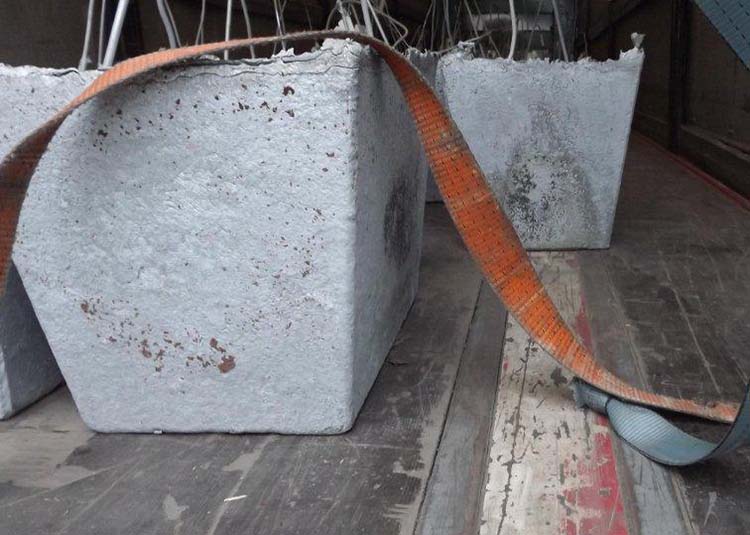
Figure 2 [Karl-Heinz Pachoinig]
In fact, it is difficult to estimate the friction forces at work in this material pairing. A tired-looking textured coated board, on the one hand, and the extremely rough surface of the (zinc?) ingots, on the other. While the right-hand ingot behind the belt is resting almost only on metal.
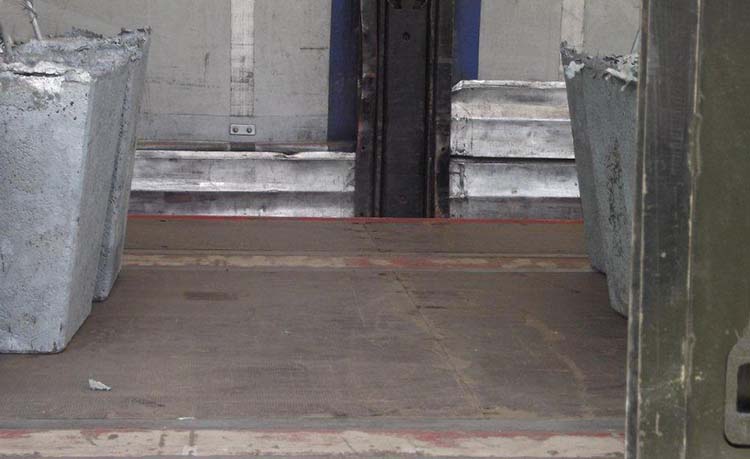
Figure 3 [Karl-Heinz Pachoinig]
So what are we left with?
An unknown friction, significant gaps in the load and a clean loading bed. Load securing measures = Zero and removable slats made from hollow aluminum sections in a dubious state. Thanks to their geometrical shape, these removable slats provide an impressive amount of strength; however, if the slats are so badly mishandled that the geometry becomes unrecognizable or is completely destroyed then their strength will not be far behind. But we say this only in passing, because this circumstance has only just grabbed our attention while looking at this photograph.
Load securing:
What would we recommend?
- First of all, we would make sure that we know the friction involved by placing anti-slip material under the entire surface of the load.
- During loading, we would place the ingots together in such a way that they have a complete tight fit to one another (even though this is only possible at the top edge due to their shape). This makes it possible to achieve better angles when lashing the load down.
Figure 4 [Karl-Heinz Pachoinig] - Because the edges of the ingots are very sharp, we would use double protection. 1. By means of protective sleeves and 2. by means of edge protectors. Since the belts are able to vibrate during transport, there is a danger that they might be damaged by the many sharp edges and that is something we need to avoid at all costs.
- Thanks to the tie-down lashings, the load is already adequately secured to the side and the rear.
- At the front, however, we still need to find 4,800 daN of securing force.
- To do this, we would choose to stow the entire load in a single block in such a way that the common center of gravity is located exactly where the load distribution curve shows it should be.
- We then attach a belt (lashing capacity = 2,500 daN) a good three meters behind the front of the load on both sides of the load block and pass it smoothly along the side forwards towards the end wall.
- Immediately next to the load block, we lay two boards pointing in the direction of travel on both sides of the load in such a way that they protrude a little beyond the front of the load.
- We then stack three pieces of squared lumber on top of one another and place them in front of the load to form an artificial end wall. The boards make sure that there is enough room for the belt and an edge protector underneath the squared lumber.
- Next, we take both belts on the right and left sides and guide them backwards towards the other side of the vehicle without twisting them, lead them past our artificial end wall and attach them very loosely at another load securing point.
- Of course, these belts have to be protected against the sharp edges of the ingots along their entire length.
- We then push edge protectors under the slack belts on both sides of the deflection points of our artificial end wall so that the force can be properly distributed between the two load securing points.
- The longer the belts are, the better the angle is but the more stretched they are if they are subjected to a load. That means that we have to find a healthy compromise of, for example, three or four meters.
- It is important for the belts to be of the same length so that they can have an equal load-bearing capacity.
- We thoroughly pre-tension the belts so that the load cannot slip into loose belts. This is because, in such a case, a braking maneuver would allow kinetic energy to develop relative to the loading bed and that is something that it is very difficult to secure a load against.
Your load securing columnists wish you a happy, safe and load-secure May!!
Back to beginning