Photo of the month – August 2020 |
[German version] |
Belt-eating banana in the vegetation
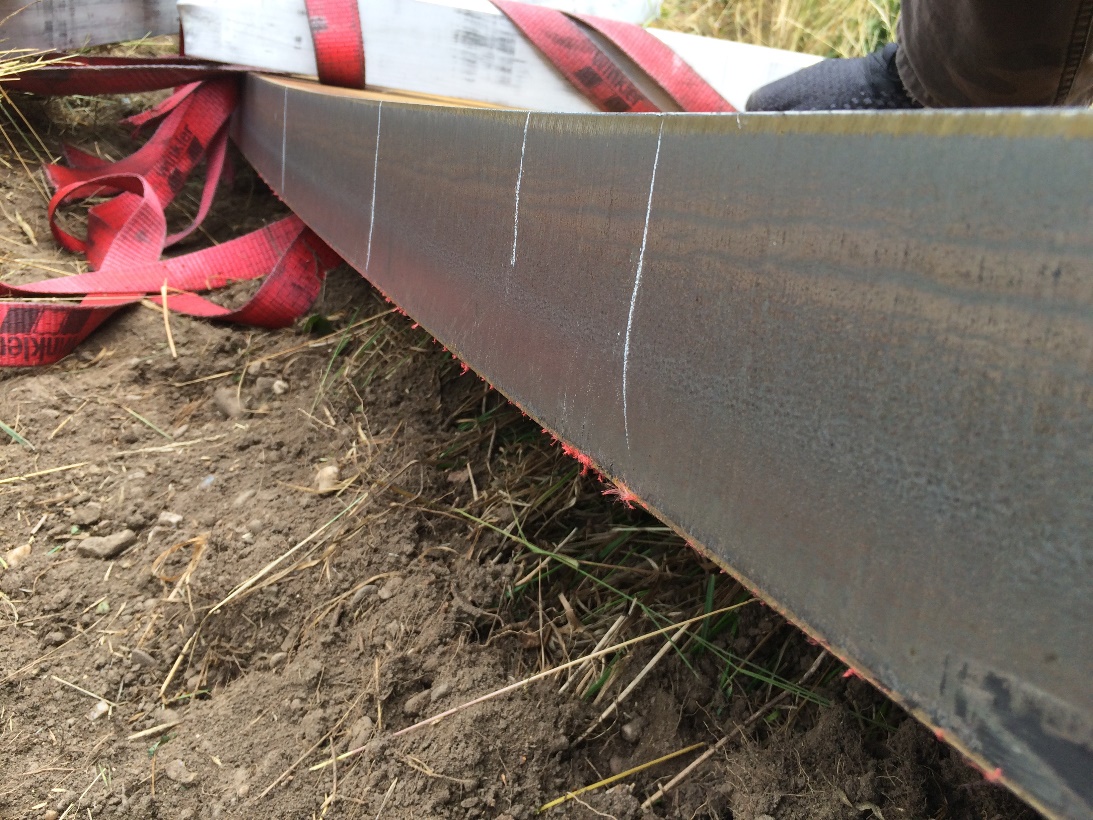
Figure 1 [Christian Freidl]
Figure 1 partially explains the title of this Photo of the Month. We can clearly see that the belt has been chewed to pieces. We think it is a very revealing photo. In principle, belts are phenomenal items of securing equipment. Compared with chains and wires, they are extremely light and easily handled. But there is no silver lining without its cloud; Even though belts do a wonderful job when securing loads, they are dreadful when it comes to their resilience against damage. When they are used, belts have to be protected against sharp edges and abrasive materials, otherwise they are of no value for securing a load. In this case, the belts had little or no value in securing the load, partly because they were not protected and partly because the securing method that was chosen made no sense, but more of that later.
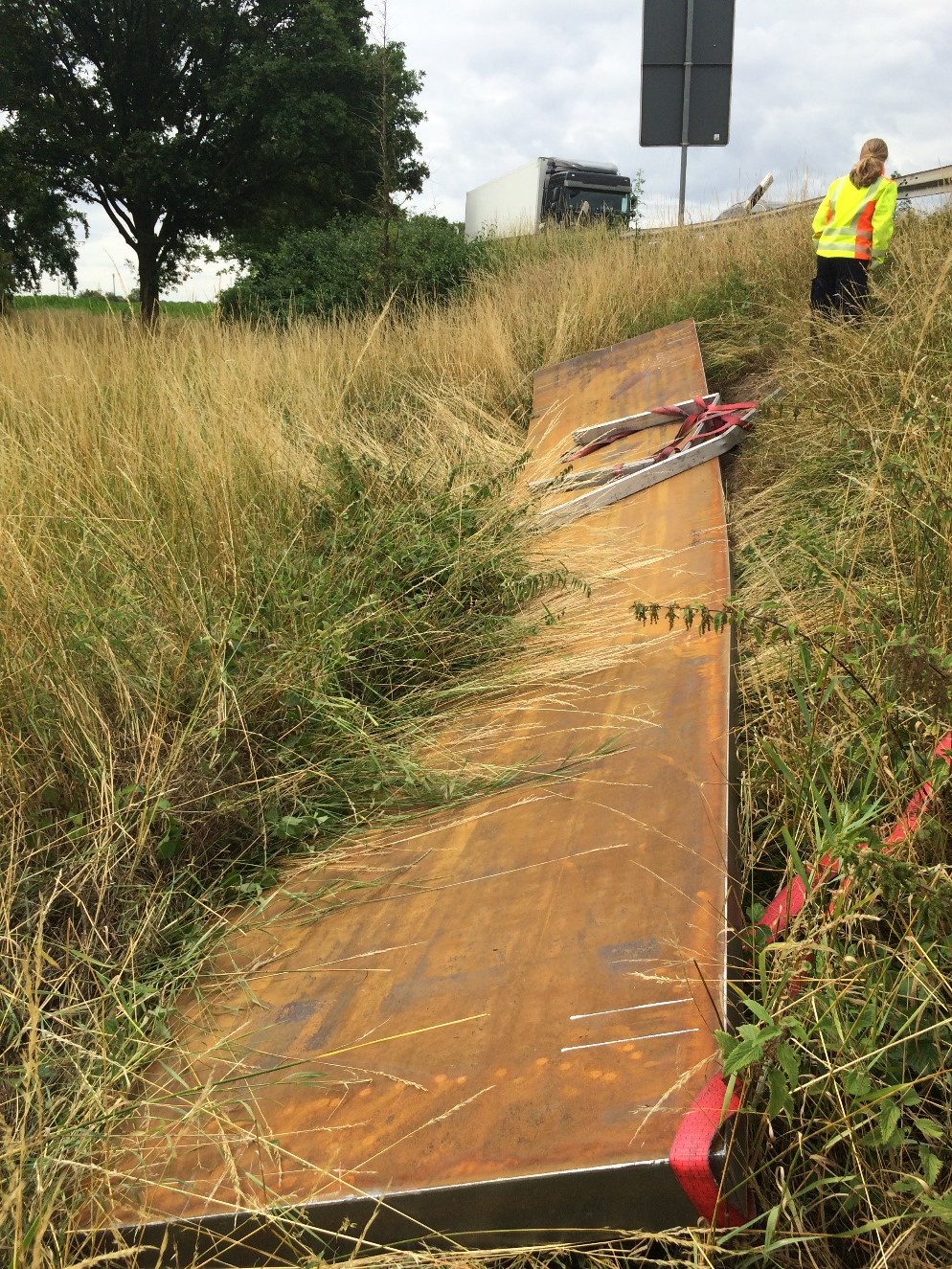
Figure 2 [Christian Freidl]
Figure 2 explains the rest of the title of this Photo of the Month. The load comprised two “banana-shaped” sheet steel elements. We chose the term “banana” to describe the slight curvature of the 100 mm thick, 9 m long sheet steel elements. They were loaded on edge and next to each other in the form of an “S”. The vehicle followed a shallow “S” trajectory (first slightly to the right, then slightly to the left, and finally to the right again to join the main carriageway). The road was sloping downwards a little. These slight “S” bends were enough to unintentionally “unload” one of the steel bananas. We don’t want to go into how a truck shedding a load like this could have cost lives if it had happened elsewhere. We shall merely acknowledge the fact and breathe a sigh of relief. What we do want to do today (and we hope we are not boring our regular readers) is to once again look in greater depth at tie-down lashings. Why? Well, let’s just take a look at the next two photos…
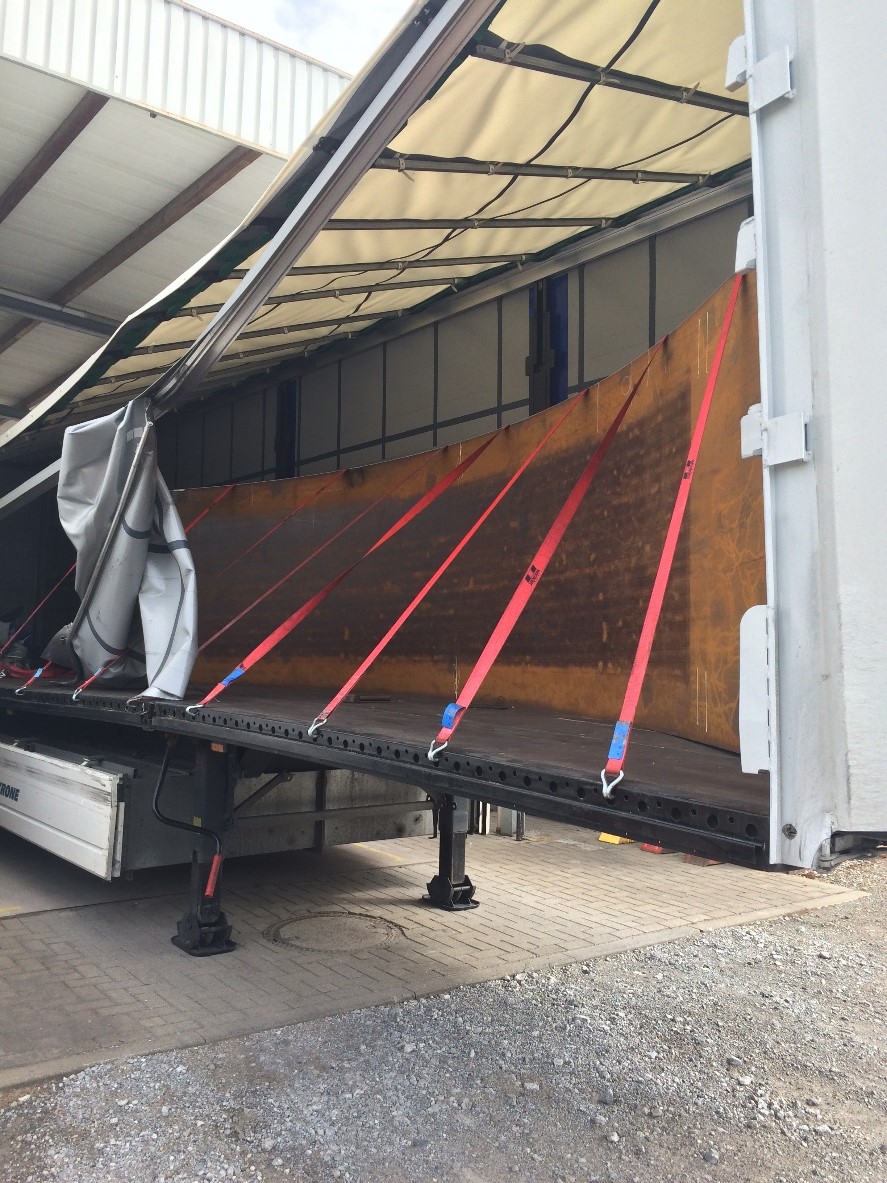
Figure 3 [Christian Freidl]
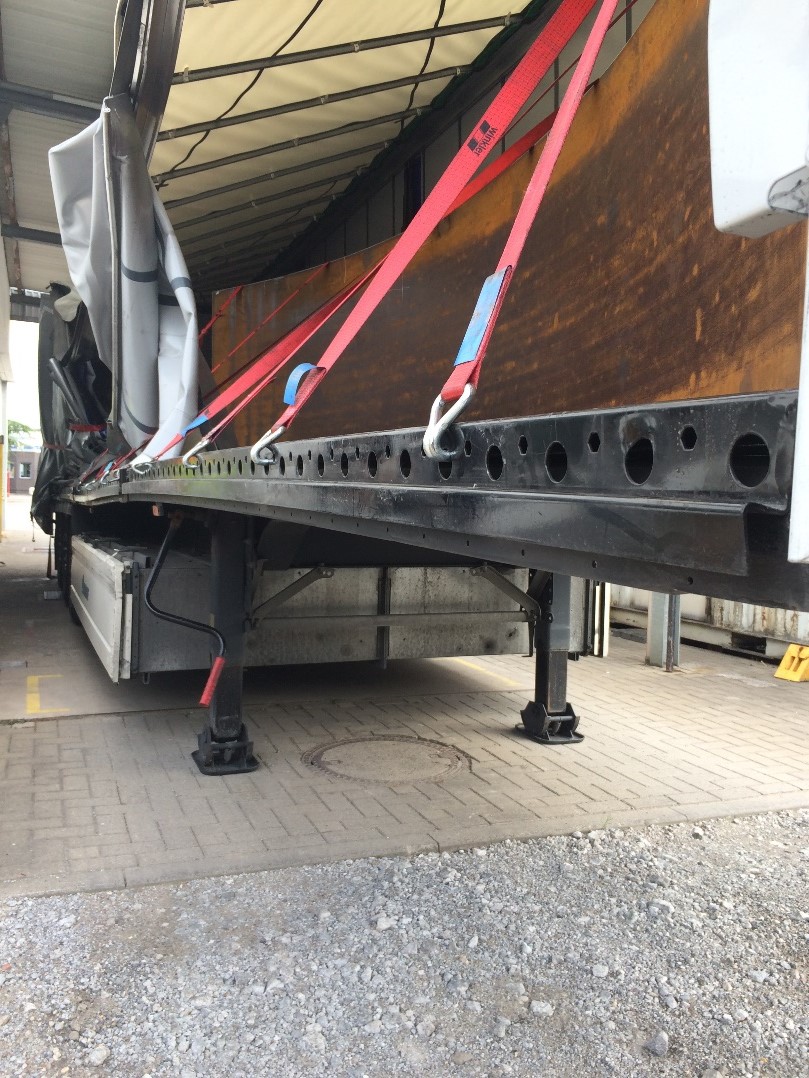
Figure 4 [Christian Freidl]
Some people, in all seriousness, had the absurd idea ….
But before we start, a word about tie-down lashings in general:
How they work: | They work by friction. The pre-tensioning force in the belt (only the vertical component) artificially increases the “weight” of the load. This means that the weight force of one steel banana is increased from 10,000 daN by around 600 daN for each belt. For this calculation, we ignored the angles and assumed a pre-tensioning force of 400 daN and the loss due to friction on the steel banana at 50 %. It goes without saying that this friction over the load itself also has a securing effect, because ‘for every action there is an equal and opposite reaction’. But this is not taken into account in the relevant directives, and so we are also ignoring it today, because it would not have made any difference with this foolhardy attempt to secure the load. |
Connection: | Hooks are used to make the connection to the vehicle. In this case, the hooks are subject to bending and opening forces. This weakens the entire system, which is unacceptable. This vehicle has holes in the frame that only allow lashing equipment to be attached more or less vertically. A load such as this would have required claw hooks that could be hooked into the vehicle frame. Alternatively, a vehicle with load securing points on the loading bed should have been used. |
Protection: | Although vitally necessary, no protection has been provided for the belts, with the result that this attempt to secure the load does not even merit the description “load securing”, and must be rejected. How could the belts be protected effectively? By using smooth edge protectors? This wouldn't really provide good protection, because the steel plate is too thin and too many protectors would be needed. A good option in this case are protective sleeves. They are not too thick and can also be passed under the plates. |
Friction: | Since tie-down lashings only work through friction, friction is of particular importance for this method of securing. Unfortunately, no anti-slip materials have been used, so we shall look at the friction pairing of textured, laminated floor (new or as good as new) in a clean condition and steel plate. No rust, hammer marks or scale can be seen on the “cut edges” of the steel. Indeed, some of the steel is shiny. We therefore assume a maximum coefficient of friction μ of 0.3. |
Securing of the load: | The steel plate was “secured” with 8 tie-down lashings. Let us for the moment disregard the fact that the belts were not protected and let us very generously assume that a vertical pre-tensioning force component of 600 daN was applied for each belt. So this meant that we had an effective securing force of 8 x 600 = 4800 daN? Of course not, because this 4800 daN only act through friction. Since we assumed a value for μ of 0.3, we have to multiply the 4800 daN by 0.3. Which leaves just 1440 daN of securing force. In the direction of travel, we need 8000 daN of securing force to secure one steel plate. 3000 daN comes from the friction of the load itself, and a further 1440 daN is provided by the tie-down lashings. This leaves a shortfall of 3560 daN. This means that we still need 20 more tie-down lashings with the same pretensioning forces and vertical components that we somewhat optimistically assumed earlier. Of course, this is nonsense: With so many belts, you would no longer even be able to see the load, and it is also questionable whether they would actually secure the load successfully. |
Assessment: | This attempt to secure the load was a gross misjudgment and misunderstanding of the laws of physics! Or perhaps the loader and the driver did not for one moment consider the danger posed by this vehicle. Such irresponsible behavior must have consequences. The first consequence is the loss of the load and the second consequence will be the prosecution of the offense and the resulting fine. If someone had been injured, it would have been a criminal offense (at least culpable bodily harm), which would have been tried in court. |
Responsibility: | The responsibility is borne jointly by the loader, the carrier or shipper and the driver. If the carrier / shipper sent the right vehicle to the customer, well equipped with load securing material, and if they did so in the knowledge that the driver had successfully completed a load securing training course, they are off the hook. The driver is always responsible when he sets off with the vehicle, because he has an obligation to ensure the operational safety of the vehicle. But, in our eyes, it is the loader who is actually responsible, because he is the one who does the loading and is in large measure responsible for securing the load. He has the necessary resources and, if necessary, he can instruct the driver and, above all, his own staff to load and secure the cargo in a suitable manner. He is in the position to prevent the driver from leaving until the load has been loaded and secured so that it is fit to be on the road, and, the way we see it, he also has the duty to do so. After all, he is the one in control. He has the task of loading the cargo so that it is safe to be transported. |
Delegation: | Attempts are often made by the loader to delegate responsibility for securing the load to the driver (the weakest party). Even if load securing is not actually the job of the driver, the loader can reach an agreement with the carrier that the driver should secure the load. Unfortunately, there are also one or two less-than-scrupulous lawyers who also wish to delegate the responsibility to the driver, i.e. the weakest party, and also document this in contracts. We can imagine a scenario in which an accident happened when transporting a load secured like this: Four dead and seven injured. On the advice of his legal counsel (the less-than-scrupulous one), the loader has delegated responsibility contractually to the carrier and his “agent” (the driver). At the loading ramp, the driver was left to secure the load on his own. Any request from the driver for assistance with securing the load in any way was rudely refused by pointing to the contract. Pick-ups at a factory are always pushed through under considerable time pressure and the way in which a load is secured is not checked at all, even though there are shortcomings as in our case here, and , indeed, this appears to be the rule. |
The question of guilt: | The driver will undoubtedly share the blame, but the court will examine whether the loader has fulfilled his obligations. If he has accepted shortcomings in load securing in the full knowledge that they are present and has not instructed the driver to rectify them, as is the case here, or if he does not regularly check the securing of the load, he will be sitting in the dock alongside the driver, no matter how much power he thought he had over him. If the responsibility in the loading company has not been delegated properly and professionally, it will be the manager that will be sitting there. And, if we may say so, that’s where they belong. We would judge the question of guilt on the basis of the degree of power exercised by each party, among other things, although this in no circumstances exonerates the driver. But we could well imagine a ratio of 10:90. |
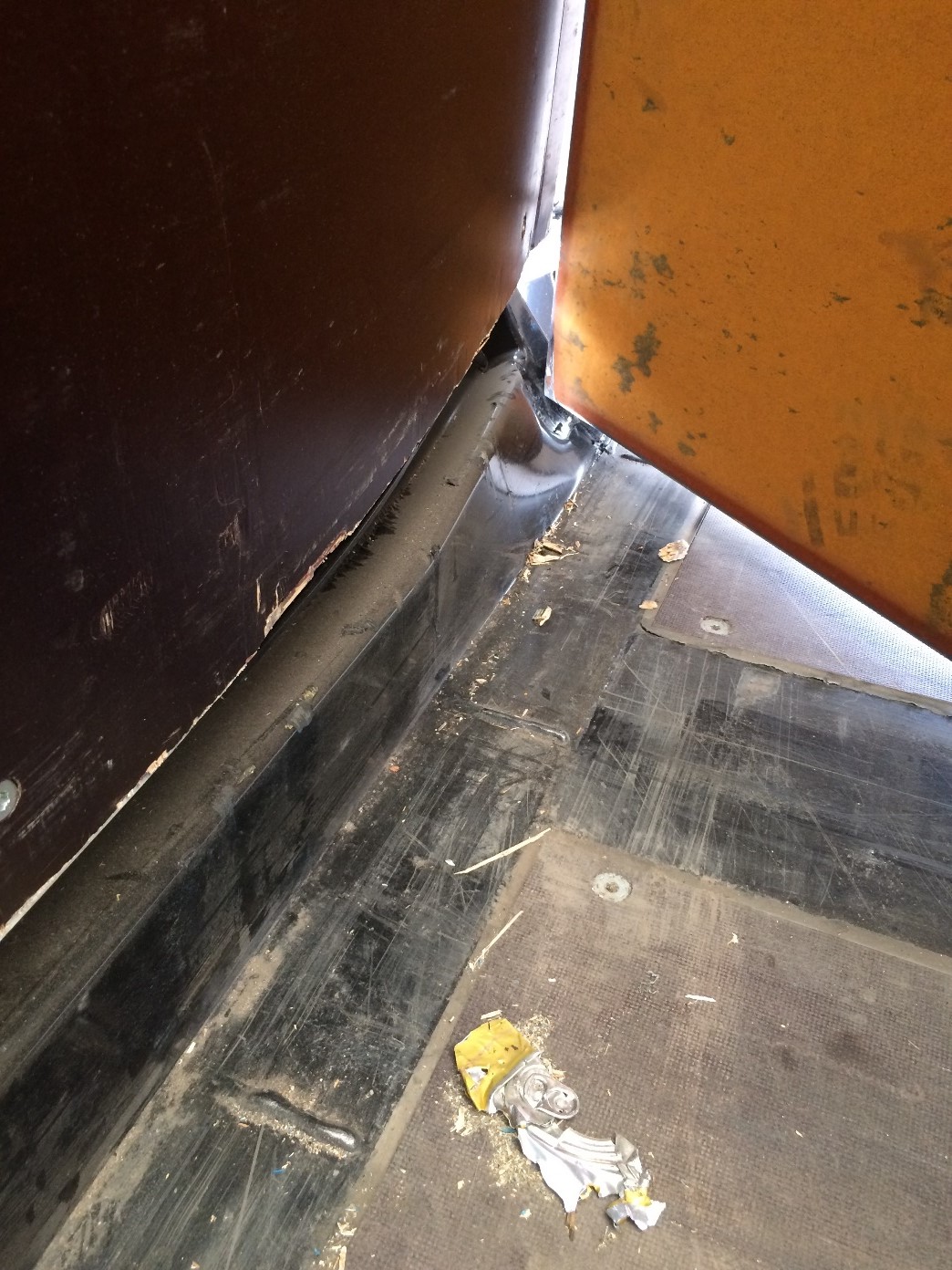
Figure 5 [Christian Freidl]
Figure 5 shows the end wall of the vehicle with the remaining steel plate. Given that one of the two steel plates was lost due to lateral acceleration as the vehicle was negotiating the shallow S bends, we could not initially explain why the second steel plate chose to ram the end wall as well. The police officer at the scene gave us his version, which makes eminent sense to us: When the driver realized that he was losing his load, he braked sharply, which is a normal reaction in such a dangerous situation. Because, as we have discussed in detail above, the steel plates were appallingly badly secured, the plate that remained on the vehicle was able to move almost unhindered during braking. It was only stopped by the end wall. Even though it was not far to the end wall, the 10 tonnes were enough to give it a good battering.
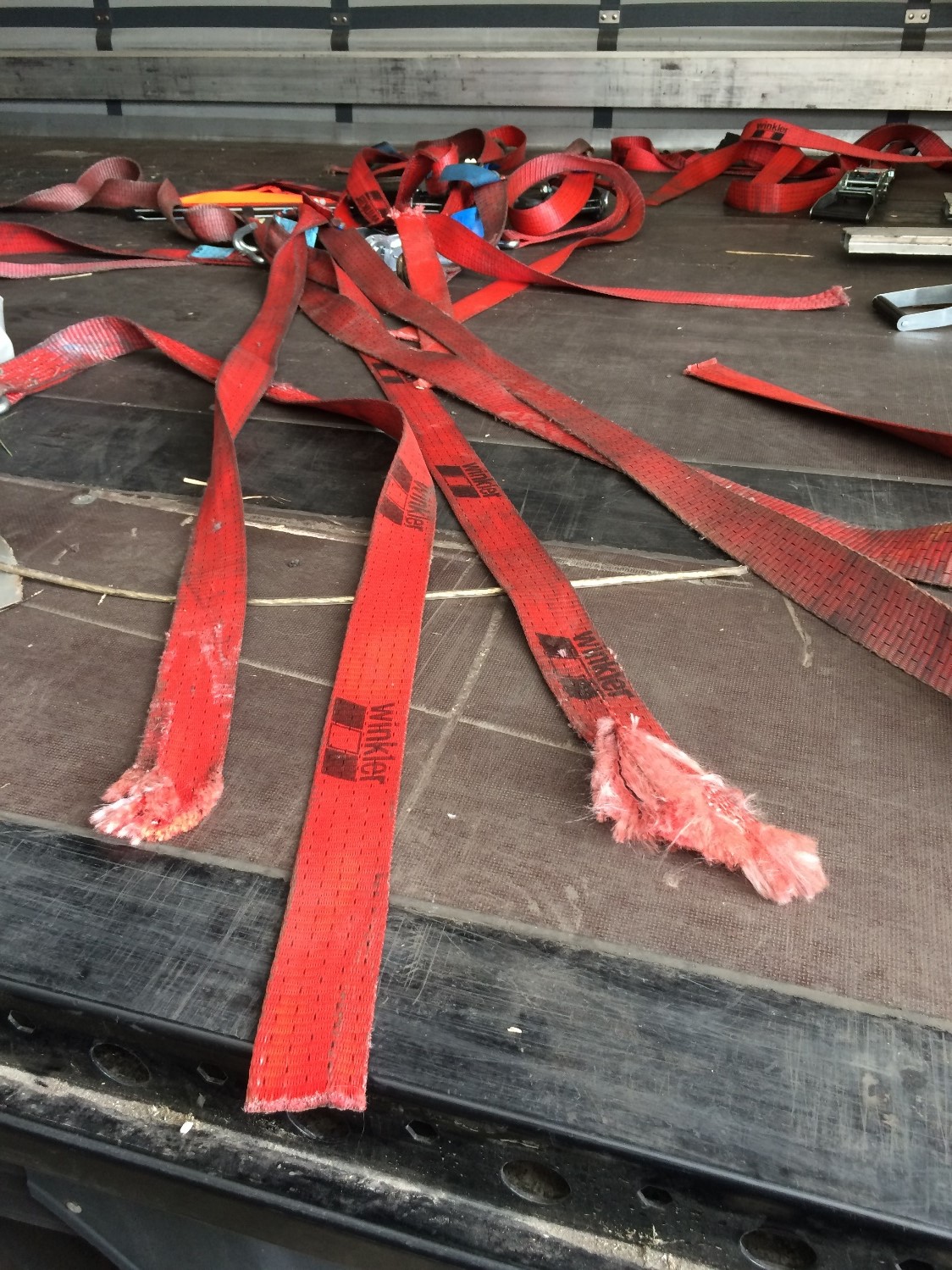
Figure 6 [Christian Freidl]
A hodgepodge of chewed and sliced belts. This photo clearly shows the weak point of the otherwise so immensely versatile and useful belts.
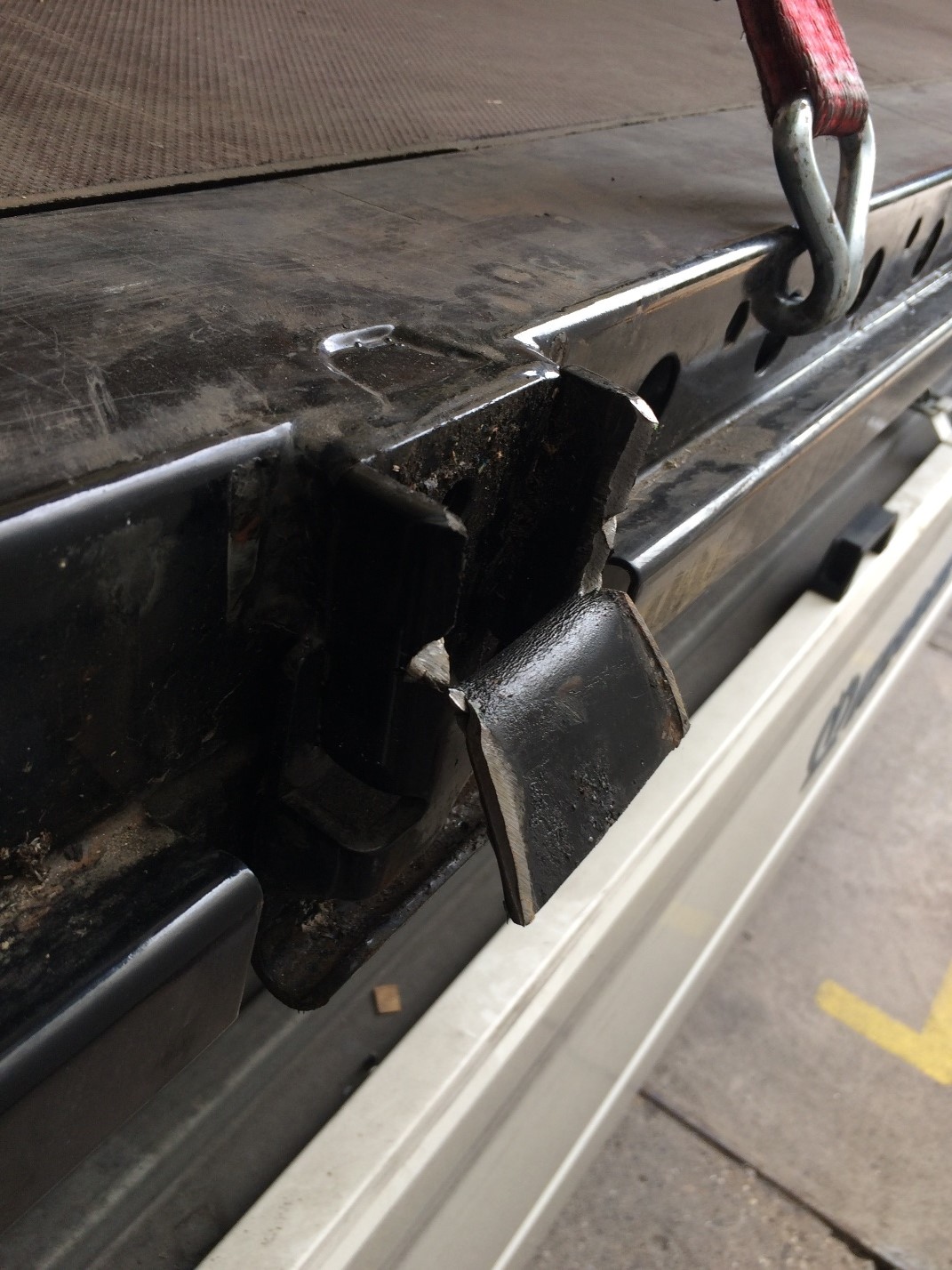
Figure 7 [Christian Freidl]
Here, the term collapsible stanchion has been taken a little too literally. Once 10 tonnes of steel are in motion, nothing is going to stop it easily as you can see from this broken stanchion pocket.
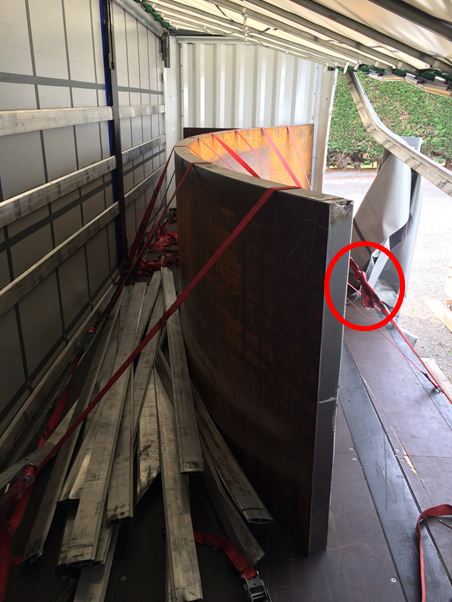
Figure 8 [Christian Freidl]
Last but not least, instead of talking about the knotted belt, which really is of no great bearing in this load-securing catastrophe, we shall consider the stability of the steel plates. Without the curvature, the question is quickly answered. However, if the plate is curved, the footprint is increased. But is that enough? Let us imagine a line from the front edge of the plate to the rear edge of the plate. Now we measure the imaginary width in the middle and add the 100 mm thickness of the plate. If the total is greater than half of the upright height of the plate, there’s no problem. If it is less, the steel banana is not stable and this has to be taken into account when it is being secured.
Securing the load:
Anyone familiar with our column can guess what's coming. And we don’t want to disappoint you:
- Friction is a magnificent thing, because it has a securing effect in all directions (to the sides, to the rear, to the front) without the need to put in a great deal of work. And so we like to use anti-slip material. In the case in hand, it should be suitable for heavy duty applications, so it should be fully vulcanized rather than a light-duty mat that is liable to crumble. These steel plates are loaded and probably also unloaded with a magnet, so there is no need to use additional wooden dunnage, as the load is distributed on the vehicle pretty well.
- As so often, direct lashings are our multi-purpose weapon against poor load securing. These loop lashings should be positioned in such a way that they take account of the curvature of the load. In other words they should be attached at the ends at around 90° to the plate itself. Since we are using anti-slip materials with a thickness of at least 10 mm, there is enough space under the plate to allow the belts (which were laid out before loading) to be moved to their final position. Because we want to guarantee that the load is secure, we recommend three pairs of loop lashings (front, middle, rear). This type of securing makes the question of the stability of the plates redundant, as the plates are adequately secured to the sides many times over by these six belts. Only one loop lashing is needed to secure the load to the front, since we can now expect a coefficient of friction μ of 0.6, leaving us to find just 0.2 for securing to the front. 10,000 daN times 0.2 comes to 2000 daN. So we shall use one belt as a loop lashing to restrain the load from moving forwards. If the angles are acute, the loss is quite small and one belt delivers twice 2000 daN minus the loss as a result of the angles, which we all agree should be kept as small as possible. So we shall use two times 1800 daN = 3600 daN in our calculations. This is plenty, provided that the sensitive belts are excellently protected from the rough edges of the steel plate. With the loop lashing used to restrain the load from moving forwards, we would even tend to use a chain, as this does not stretch as much. This means that the steel plate does not have to slip as far before it is held securely by the tensioned chain.
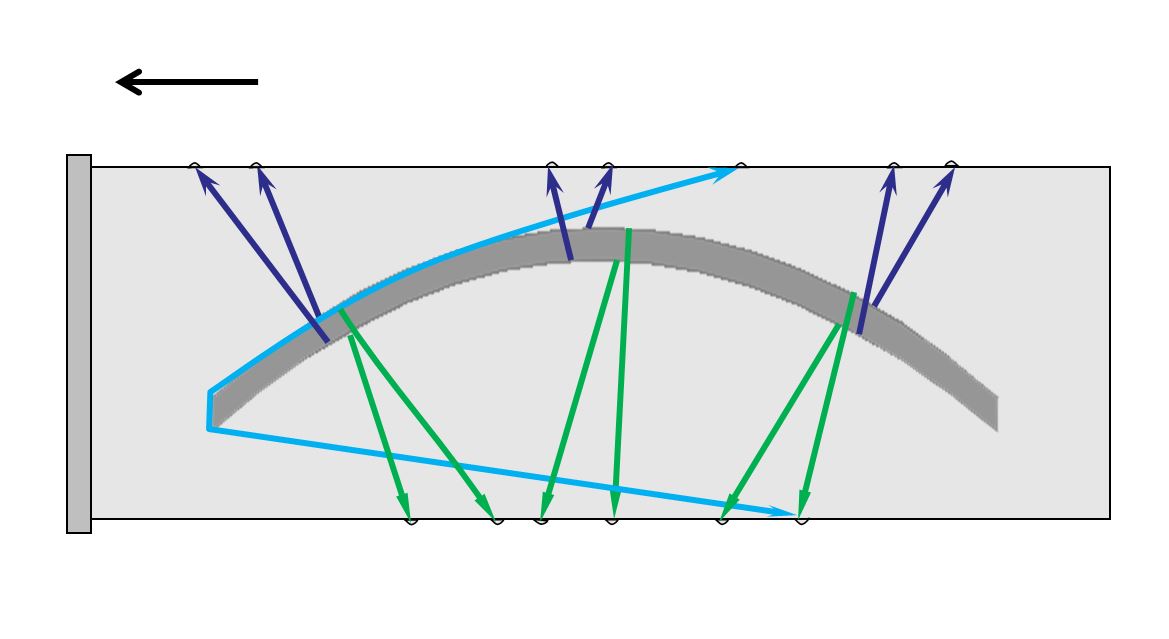
Diagram 1 [GDV]
Your load securing columnists wish you a safe and secure summer.
Back to beginning