Photo of the month – February 2010 |
[German version] |
A narrow escape … or "pick-up sticks" for adults
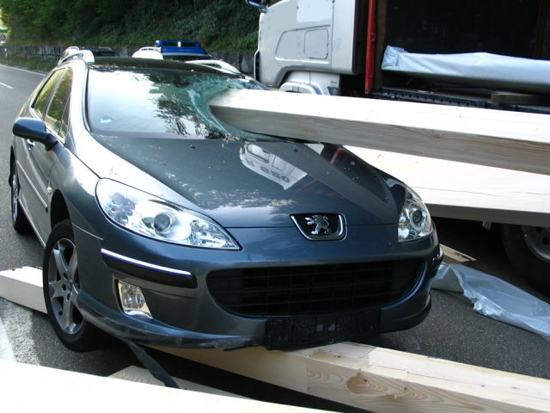
Figure 1 [Gerald Wiesner]
An articulated truck drove round a right-hand bend. In this bend, the vehicle lost part of its load. An oncoming car was not able to take avoiding action and collided with the load. The load was made up of laminated trusses. One truss smashed through the windshield and penetrated the interior of the vehicle.
The driver of the car was extremely lucky! When we asked her, she told us that the road she was driving on was an uneven road with poor visibility. Figure 5 shows that the articulated truck was coming towards her from the bend. When it came into sight, the wooden beams fell from the loading area in slow motion and slowly slipped onto the road towards her. It is thanks to the drivers quick grasp of the situation and rapid reactions that this lost load did not turn into a fatal accident. She ducked to the right onto the passenger seat while her car rode up a little on one of the beams.
The "only" injury she sustained was a slight injury to her left hand. It doesn’t take any imagination to envisage what would have happened if she had not been able to react so quickly. Figures 1, 2 and 3 clearly show that the laminated truss penetrated the windshield exactly at head height and exactly above the driver’s seat.
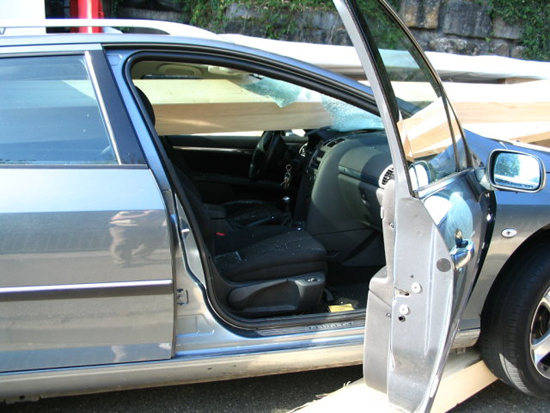
Figure 2 [Gerald Wiesner]
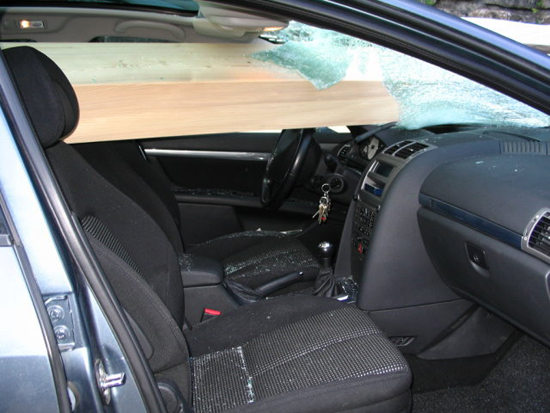
Figure 3 [Gerald Wiesner]
So what led to this dangerous event?
Several laminated trusses were being transported on the platform of the articulated truck. They were of different cross-sections and were wrapped in plastic film in pairs. Three of these packages were resting on squared lumber, and the figures show that this squared lumber had a square cross-section. No friction-enhancing materials were to be found under the squared lumber or on the squared lumber and under the film-wrapped laminated trusses.
On top of this first layer were three further packages of trusses, that were also film-wrapped. In this case, the friction pairing was film on film. The film was very smooth, so that it can be assumed that the coefficient of friction µ was a maximum of 0.2.
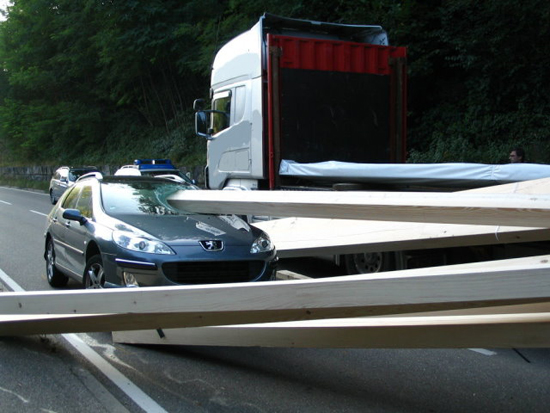
Figure 4 [Gerald Wiesner]
According to those involved, the load was "secured" using tie-down lashings. It is not quite clear whether two or three lashing belts were used. The lashing belts had a lashing capacity of 2500 daN and the labels on the long-lever ratchet tensioners used showed an STF of 500 daN. The load was nowhere loaded as a tight fit (see figure 10).
The total weight of the laminated trusses was around 3,000 kg.
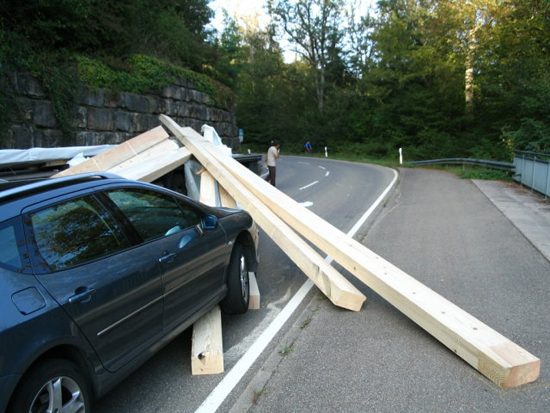
Figure 5 [Gerald Wiesner]
What was the required securing force?
To adequately secure the load, the following minimum securing forces are needed:
To the front: | 0.8 x load weight = 0.8 x 3000 = 2,400 daN |
To the sides and to the rear: | 0.5 x load weight = 0.5 x 3000 = 1,500 daN |
Because the load was nowhere loaded as a tight fit, all the securing force must be achieved by frictional forces and the tie-down lashings.
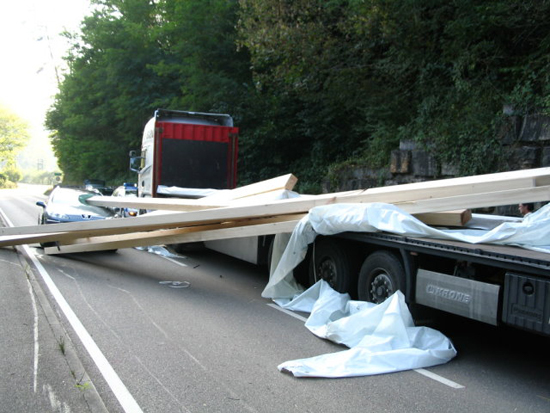
Figure 6 [Gerald Wiesner]
What securing force was present?
The coefficient of friction µ was restricted to 0.2.
This means that 0.2 times the weight of the load is secured by friction. In this case, that equates to 600 daN. If three lashing belts were used, the following calculation applies:
STF = 500 daN x 3 = 1,500 daN x 1.5 (K value) = 2,250 daN x 0.2 (friction) = 450 daN
This means that the belts deliver a total securing force of 450 daN. And this does not even take into account that the belts were not tensioned at the ideal 90° angle, which causes a further loss of securing force. Friction and lashing forces therefore deliver a total securing force of 1,050 daN. This means that there is a shortfall of 1,350 daN in securing force to the front and to the sides and of 450 daN even to the rear.
This calculation assumes that the load securing equipment was optimally pre-tensioned and was tightened during transportation. However, this columnist’s extensive experience from daily vehicle inspection operations suggests that neither of these assumptions are reliable.
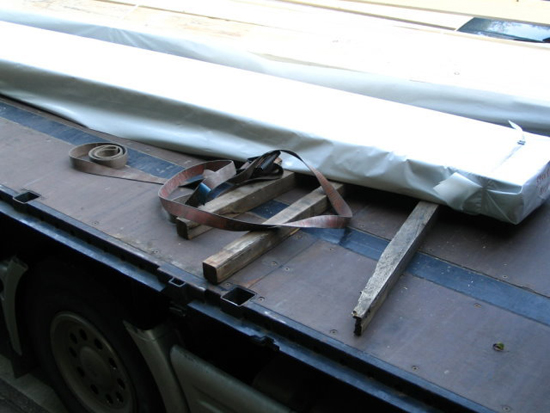
Figure 7 [Gerald Wiesner]
It should therefore come as no surprise that this load broke free. The poor road was sufficient to cause the laminated trusses to slip from the loading area as a result of the constant vertical jolts.
It is possible that the driver braked slightly just beforehand, so that squared lumber placed on end tipped and the lashing belts therefore immediately lost their pre-tensioning force. If, for reasons unknown to us, it is necessary for loads like this to be transported on edge, then steps must be taken to ensure that they cannot tip over. If just one beam tips under the belts, the belts lose their pre-tensioning force and the load is resting unsecured on the loading area.
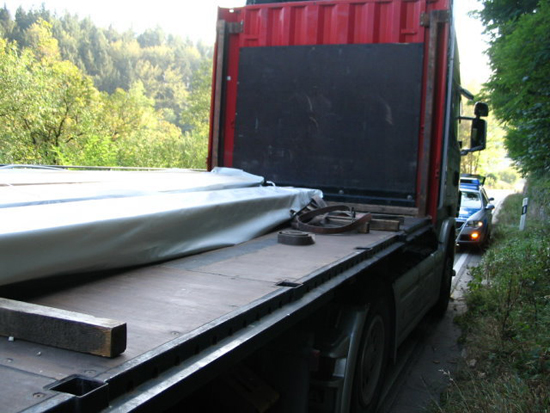
Figure 8 [Gerald Wiesner]
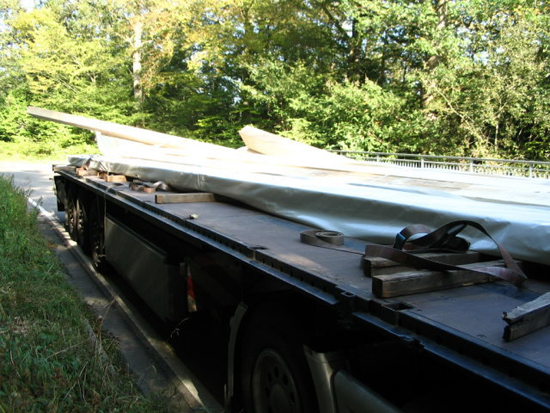
Figure 9 [Gerald Wiesner]

Figure 10 [Gerald Wiesner]
The square beams were fanned across the loading area after the event. They either slipped, or they could even have rolled, because, as has frequently been said loud and clear in this column, squared beams with square cross-sections have a tendency to roll.
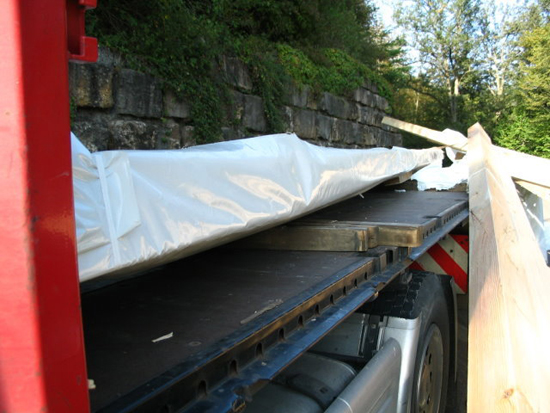
Figure 11 [Gerald Wiesner]
How can this load be secured simply, quickly and adequately to prevent an event such as this?
![]() |
Commandment 1 | – | Ensure a clean loading area. |
![]() |
Commandment 2 | – | Increase friction. |
![]() |
Commandment 3 | – | Load the cargo as a tight fit to the front. |
![]() |
Commandment 4 | – | Place any rectangular squared lumber supporting the load with the wide face to the loading area. |
![]() |
Commandment 5 | – | Avoid squared lumber with square cross sections supporting the load (because they tend to roll) |
![]() |
Commandment 6 | – | Bundle the load so that it cannot tip under the belts. |
If you observe all these "commandments", this load is simple to secure.
Friction-enhancing mats must be used. With a coefficient of friction µ of 0.5 these are sufficient to secure the load if it is loaded as a tight fit to the front. The minimum securing requirements then demand that two tie-down lashings are used to ensure that the high frictional forces are maintained throughout the journey.
It only remains for us to wish the driver that she never encounters a situation like this again. The driver of the articulated truck will certainly remember this accident every time he loads up his truck. Our wish for him is that his loads never again represent a hazard for road safety.
Back to beginning