Photo of the month – November 2007 Version 1.0.0.07 |
[German version] |
"Cans festival"
Packaging, the formation of cargo units and load securing go hand in hand. Good packaging, correctly executed, is the prerequisite for economical and sound load securing.
The demands on the packaging are high, as it has to perform a variety of functions. In the case illustrated here, it is the protective function of the transport packaging that has quite clearly failed.
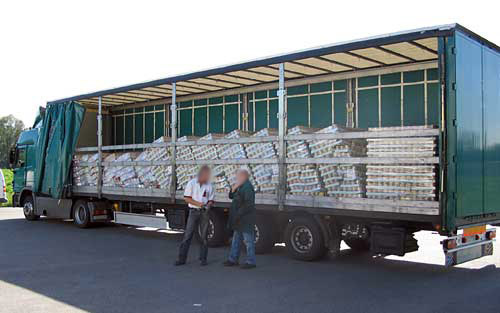
This example clearly illustrates that the packaging has to be designed to protect the package contents against any loads that they may be subject to across the entire distribution path. The reason is simple: The more difficult it is to secure the package or transport packaging in the cargo unit, the more effort needs to be expended to secure the cargo unit in the vehicle properly.
Anyone who introduces a load onto the public highways is generally responsible for ensuring that it is loaded in a manner that makes it safe to transport. The shipper and their agent, on the other hand, are responsible for ensuring that loading is carried out in an operationally safe manner.
For the purposes of this example, we shall desist from splitting the undoubtedly interesting semantic hairs of precisely what it is about this load that is "safe to transport" and what is "operationally safe". For this discussion, it is sufficient to note that a straightforward braking maneuver was sufficient to put the load in the state we see in the photographs.
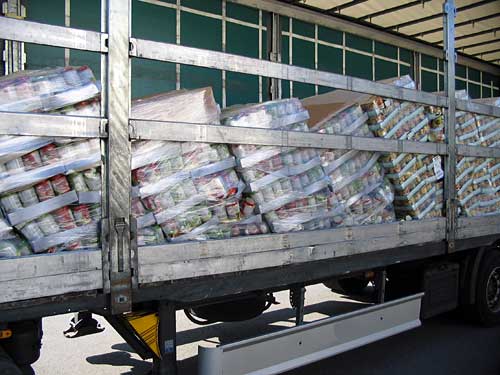
The load is made up of cans and some conical containers (possibly screw-top jars) covered with plastic film. These containers were packed in open boxes and the boxes were stacked on pallets. The cargo unit was then "secured" with stretch film and some intermediate layers.
Securing of the cargo unit was indubitably insufficient, as the cargo units were so "soft" that they were able to shift and come apart during braking. It is probable that gaps in the load promoted such movement. Load securing measures can be sought in vain!
The driver and all other road users that were in the vicinity at the time can count themselves lucky that the vehicle was not also cornering at the time – that would almost certainly have resulted in large-scale "contamination" of the roads around the area with cans of soup.
In this example, the benefits of cargo units, namely fast and easy transshipment, have entirely vanished. Instead, not only has the cargo been damaged and delivered late, but the cans must all be laboriously unloaded and new cargo units must be formed.
How is it possible to improve securing of the cargo units in this case?
![]() |
An intermediate layer of strong cardboard can be inserted between each layer to stabilize the cargo unit. Some intermediate layers had been used in the example, but these were not sufficient to adequately secure the unstable load. |
![]() |
The sliding friction coefficient of the intermediate layers should be as high as possible (μ > 0.5). A wide range of coatings are available to increase the friction. |
![]() |
The corners of the cargo units can be strengthened by corner pieces to allow the units to be strapped horizontally or vertically with plastic or steel straps. |
![]() |
If the corner pieces incorporate the pallets, this further increases the stability of the cargo unit. |
![]() |
Suitable shrink film can also be used in place of plastic or steel straps to secure the cargo unit. |
![]() |
Covering the top layer with a pallet or plywood board firstly allows the unit to be strapped and thus improves stability and secondly improves the options for securing the load in the vehicle. |
Because the cargo units are still not entirely stable despite the measures listed above, a vehicle with a suitable body should be used. It must allow the cargo units to also be secured to the sides as a tight fit.
The first three or four rows of pallets can be secured directly in the form of a tight fit against the load-bearing end wall in the direction of travel. As of this point, with unstable cargo units such as this, it is necessary to absorb the forces that build up during braking. This could be done using a vertical plywood board or pallet etc. combined with a belt arranged as a loop lashing (bight) around the board.
The sketch below illustrates this option. For the purposes of clarity, securing to the side, for instance using tie-down lashings, has not been shown:

The belt can be prevented from slipping off using a pallet or similar. The belt should be attached at approximately the height of the center of gravity. Depending on the stability of the cargo units, forces should be absorbed in this way three or four times. The load can also be secured to the rear using a board and one or two belts (depending on the weight of the load).
If it is not possible to secure the load to the side as a tight fit, the cargo units must be formed in such a way that they can be secured with tie-down lashings, for instance. In the case of the cans, it ought to be possible to secure the load in this manner. It is not possible to state here whether the shape and sliding friction coefficient of the screw-top jars would prevent the use of tie-down lashings or not.
The ideal solution would be cargo units formed from stable transport packages, stowed in an interlocking manner and stabilized with intermediate layers of friction-enhancing material (e.g. suitably coated paper).
The transport packages used should meet the requirements of modularity, in other words, they should fill up the pallet without protruding or falling short of the edge. All the corners should then be fitted with corner protectors to allow the unit to be strapped or covered with shrink film.
A cargo unit formed in this way can then be loaded as a tight fit. Minimal securing using one tie-down lashing can be achieved for several cargo units at once using large lashing rails (angled rails).
In addition, the height of the package on the pallet can be reduced to further increase the stability of the cargo unit. It would thus be possible, for instance, to pack the pallets in accordance with "CCG I". This would approximately halve the overall height of the cargo units and significantly improve stability.
To make the best possible use of the transport space available, the cargo units could then be stacked, bearing in mind that the permitted stacking crush pressure of the transport package must not be exceeded.
Back to beginning