Photo of the month – June 2006 | [German version] |
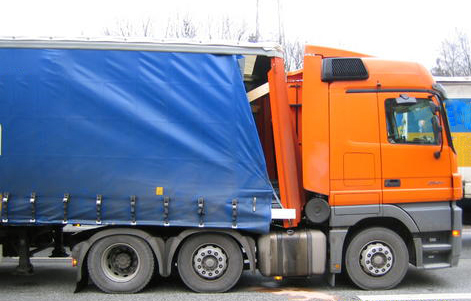
Figure 1 [F. Baumeister, VD 4, Hamburg]
Battering ram on board!
An articulated truck (the trailer was a curtainsider) had to brake from a speed of 50 kph due to a "lapse of concentration" in roadworks. The occupants of a police car which happened to be nearby only heard a bang. Initially, the officers were expecting a pile-up, but they hunted in vain. The load in the curtainsider had "rammed" the head board and separated it from the trailer. The compressed air hoses for the brakes were torn off, which caused the brakes to lock, bringing everything to a standstill. The fire service had to load the cargo onto another vehicle where it stood in order to be able to recover the truck.
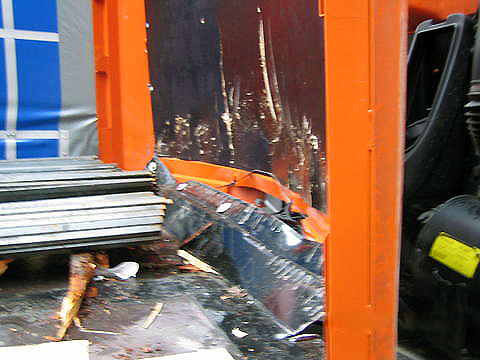
Figure 2 [F. Baumeister, VD 4, Hamburg]
The load in the curtainsider comprised 21 bundles of steel profiles, each bundle weighing approx. 1.1 metric tons. These bundles were resting on square cross-section lumber, which was also slightly icy. Load securing measures comprised three tie-downs. The braking maneuver caused the steel bundles to slip forwards around three meters before they hit the head board.
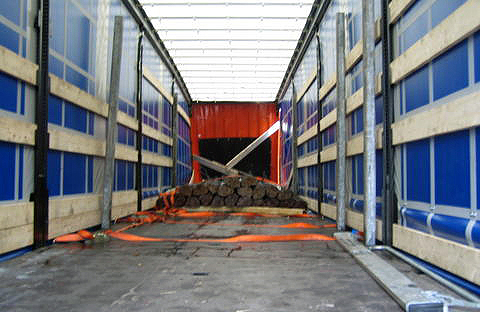
Figure 3 [F. Baumeister, VD 4, Hamburg]
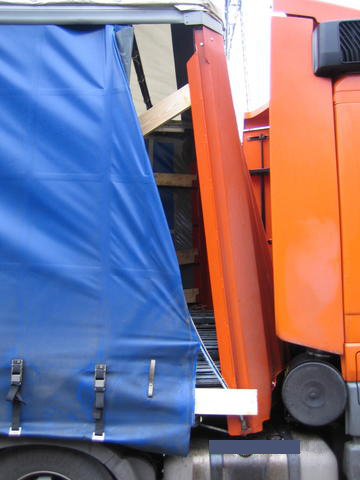
Figure 4 [F. Baumeister, VD 4, Hamburg]
Assessment by the Königsberg load securing committee:
![]() |
Square lumber tends to roll when under load. The use of rectangular cross-section lumber would have been far more advantageous in this case, as rectangular lumber does not tend to roll. Caution! The lumber must be placed with the wide face down. |
![]() |
Tie-downs only work on the basis of friction. The coefficient of friction µ between steel profiles and between steel profiles and wood can generally be assumed to be between 0.1 and 0.3, depending on the surface (rust, grease, scale, etc.). This is not a particularly auspicious starting point for securing 21 tons of steel. |
![]() |
Because the bundles are relatively loose, this type of load makes tie-down securing virtually impossible. Vibrations, oscillations and acceleration forces, etc. can cause the load to settle during transport, which would cause the tie-downs to lose their prestressing. |
![]() |
The selected securing method was unsuitable. Given the conditions, the driver would have had to use in excess of 70 belts. |
Possible load securing option:
The load distribution plan is consulted when positioning the load. If possible, the profiles are set down between the square stanchions that can be clearly seen in the figure. On the loading area, three or four pieces of rectangular lumber are distributed across the length of the profiles, each having nonslip mats on the top and bottom.
Three lashings are prepared prior to loading. Three belts are attached on each side and passed to the opposite side. After loading, these belts are passed back over the load, attached and pretensioned slightly. After the first load has been loaded as a tight fit, three or four pieces of rectangular lumber, each having nonslip mats on the top and bottom are again laid on top of this layer and the second layer is loaded.
A wooden barrier is built in front of the load. This can be done by stacking balks in front of the load-bearing stanchions. In the middle, the load can be braced towards the head board or the barrier can be "supported" by two lashings. If such loads are regularly transported, it would make sense for a movable steel or aluminum head board to be used. This can also be supported by load-bearing stanchions or in perforated battens. Some trailer manufacturers are already offering solutions of this type. Securing against the direction of travel is provided by the friction of the nonslip mats. Minimal tie-down securing in order to reduce oscillations is provided by the lashings.
Back to beginning