Photo of the month – December 2003 – Special 3 | [German version] |
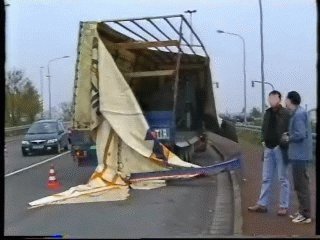
Figure 1 [T. Pempelfort]
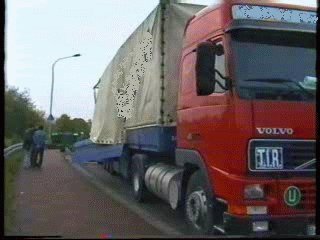
Figure 2 [T. Pempelfort]
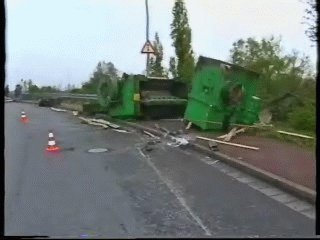
Figure 3 [T. Pempelfort]
Unloading machine parts in a bend:
A typical accident scene. A long bend to the left generates acceleration perpendicular to the direction of travel with the result that the load leaves the load area.
Basic requirements:
According to the VDI guidelines, the load should be secured against forward acceleration of 0.8 g and lateral acceleration (and rearward accelaration) of 0.5 g. The load securing must be able to withstand such acceleration (regardless of how long it lasts, i.e. including a long bend to the left/right). And it must do so repeatedly, no matter whether the truck is travelling from Hamburg to Bremen or from the North Cape to Sicily. A conscientious driver should check the securing of the load frequently during the journey to ensure that all the requirements are still met.
The vehicle:
In principle, this is a very suitable vehicle. A drop deck trailer facilitates a tight-fit at the front for at least the heaviest parts, and makes securing the load easier. Insofar as sufficient load securing points are available across the loading area and these are intact, and the vehicle has sufficient load securing materials, then this vehicle is suitable to carry out the transport.
What’s the problem?
The sacks of "cat litter" at the scene of the accident suggest that the machine parts have lost oil. Oil is often lost from the hydraulic lines. If a truck often carries machine parts on its loading area, residual hydraulic oil can escape from the hydraulic lines and connections and, if the loading area is not all that new, will penetrate the loading area. A film of dirty oil thus builds up on the loading area, the consequences of which are only rarely recognized. This particular type of loading area contamination can reduce the frictional coefficient to an absolute minimum (practically zero). Thus, the extent of the necessary load securing measures at the sides and towards the front (insofar as there is no tight-fit to take the load) must be great enought to compensate for this. The normal tie-down method is of no use for load securing in this case, since a frictional force which barely exists in the first place cannot be increased by applying tie-downs.
The only thing that remains to be said is that these machine parts are suitable for direct securing using wooden bracing, belts or chains, and that it is difficult to believe that this has not been done.
Increasing friction:
If the loading area has not been contaminated with oil, measures to increase the friction can sensibly be used in order to achieve good load securing.
Back to beginning