Photo of the Month – May |
[German version] |
Photo of the Month – Be part of it!
Dear readers of our column “Photo of the Month”,
We are extending the content of this column to include all aspects of loss prevention in the transport field. In the future, we will look not only at the risks that occur during road transport but will also turn our attention to load securing and safety across all modes of transport – whether road, rail, waterborne or airborne. We will also take the opportunity to investigate challenges such as transshipment processes and lifting technology . At the same time, we want to draw attention to positive examples that clearly illustrate proven solutions and best practices.
The material you send us is a valuable resource for us: Through your photos and contributions, you provide us with valuable insights drawn from practical experience, shed light on current developments, and stimulate the exchange of information between industry professionals. You are warmly invited to send us your ideas, sources and photos at marc.sommerfeld@gdv.de.
Let’s work together to highlight the importance of safe transport processes and raise awareness for proven loss prevention measures.
Best regards,
Your GDV transport team
Photo of the Month – May
Looks harmless, but a real problem – When load slippage halts rail transport.
To kick off this new “Photo of the Month” series, we received a number of photos from Switzerland.
At first glance, the container seems to be undamaged (Figure 1). You might well think that it has only recently been loaded and locked. But in actual fact, it has already completed a part of its journey.
A look inside the container (Figure 2) also reveals no sign of damage. The load consists of PET bottles that are being sent for recycling.
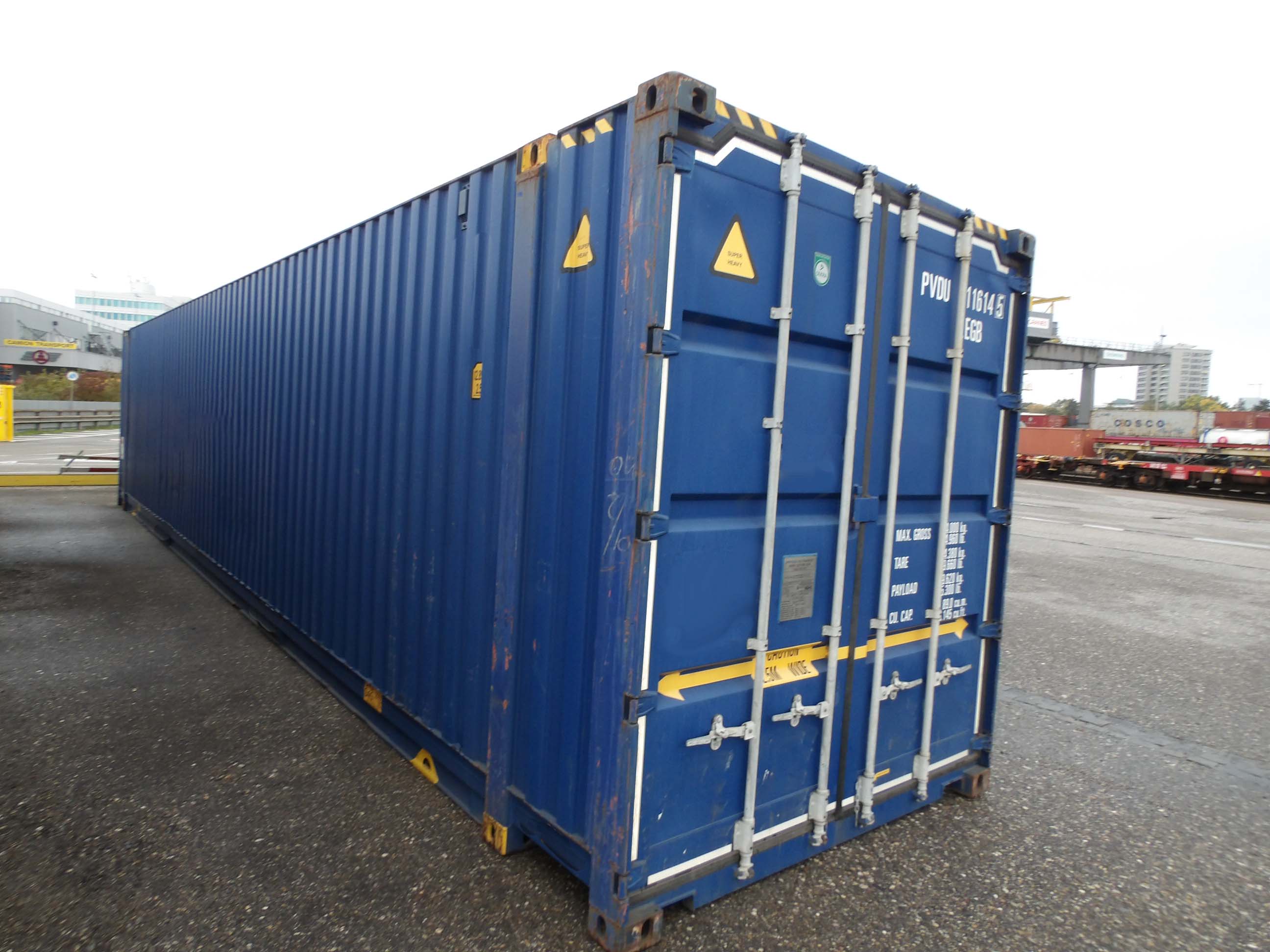
Figure 1 [Double S Solutions AG]
However, we are immediately struck by the large gap on the right-hand side of the container. According to the information at our disposal, the load shifted while being transported – but without causing any visible damage to the cargo or the container.
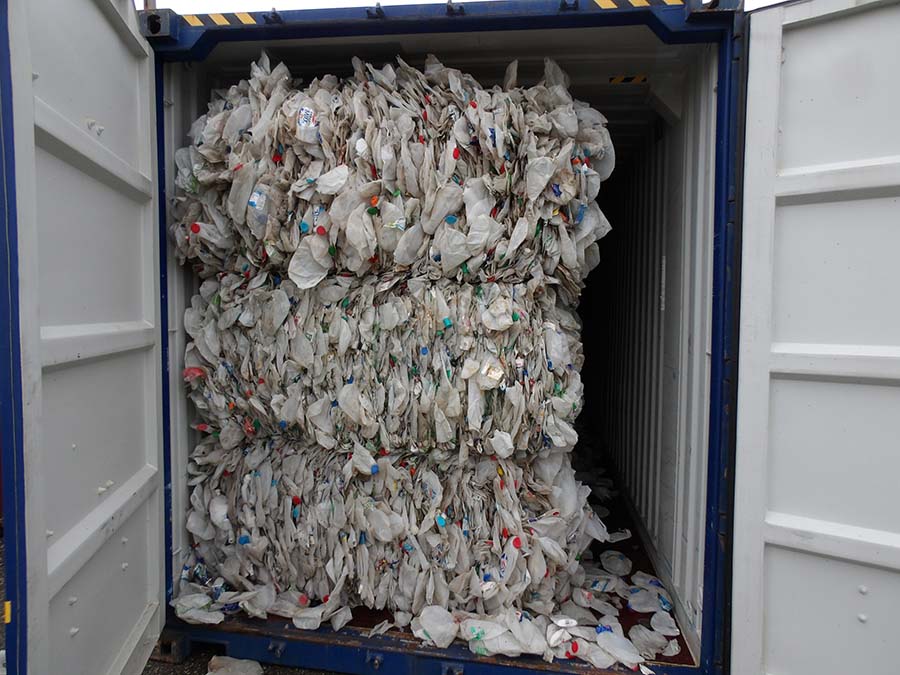
Figure 2 [Double S Solutions AG]
Where is the problem?
The problem is not one of conventional material damage. Instead, it lies in the nature of the identified imbalances. As the PET bottles moved, the weight inside the container shifted, leading to uneven loads bearing on the axles of the railway wagon.
In Switzerland, a lot of freight is transported by rail. The rail operators monitor not only the axle load of their trains, but also the wheel load at the individual axles in order to identify any imbalances between the wheels on the right-hand and left-hand sides.
Clearly, the rail operators consider these uneven loads to be a safety risk – in particular when passing through tunnels. That is why any wagons affected by this problem are excluded in a so-called “intervention yard” located ahead of the tunnel entrance. In the case we are looking at here, the operator determined that the loading either had to be improved or that the cargo had to be reloaded.
The consequences
Even though neither the container nor its cargo were damaged, the identified imbalance led to considerable inconvenience and various organizational measures:
- Unloading of the container from the wagon
- Detention charges for the container
- High cost and effort involved in unloading and reloading the PET waste
- Additional load securing measures
- Period spent in workshop by the affected railway wagon for technical inspections
These measures caused delays and led to additional costs even though there was no damage to the cargo itself.
The amount of the loss was approximately €15,000.
How could this incident have been prevented?
The identified imbalance was caused by the incorrect way the container had been loaded. Correct loading would have prevented the problem from occurring. A look at the IMO/ILO/UNECE Code of Practice for Packing of Cargo Transport Units (CTU Code) shows exactly how the cargo should have been loaded.
1. Position the center of gravity correctly
This is described in Chapter 9, Point 9.1 of the CTU Code:
“The packer should ensure that […] restrictions for the eccentricity of the centre of gravity are complied with […].”
This means that the cargo must be stowed in such a way that the container does not become unbalanced
The procedure is indicated in more detail in Annex 7, Point 1.11
“In longitudinal direction the centre of gravity of the packed cargo should be within allowed limits. In transverse direction the centre of gravity should be close to the half width of the CTU.”
The problem here was that the PET bottles were not evenly distributed, causing their center of gravity to shift to one side. This resulted in an uneven wheel load at the wagon.
What “close to” means in practice is defined in Annex 7, Point 3.1.4:
“[…] The eccentricity of the centre of gravity of the cargo should not exceed ±5% in general. […]”
In this case, the container should have been loaded in such a way that the center of gravity was not offset from the middle of the container by more than 5 % of the container width.
In numbers, this means: Given the external container width of 244 cm, the center of gravity should not have been more than 12 cm away from the middle of the container.
3. Additional load securing measures to prevent slipping
Even if the container was initially loaded correctly, this incident shows that the cargo moved during transport. Additional load securing measures should have been undertaken to prevent this.
These include:
- Cargo loaded as a tight fit: The PET bottles should have been arranged in such a way that they could not move freely, for example using transverse or longitudinal beams.
- Non-slip material under the load: The use of anti-slip mats or intermediate layers would have reduced the movement of the cargo.
- Lashing materials: Belts or nets would have made it possible to retain the PET bottles in place and prevent them from accumulating on one side of the container.
Appendix 4 of Annex 7 contains a diagram that helps users calculate the correct center of gravity (Figure 3). The presentation indicates the procedure in the container’s longitudinal direction. The same method can be used to calculate the center of gravity in the transverse direction.
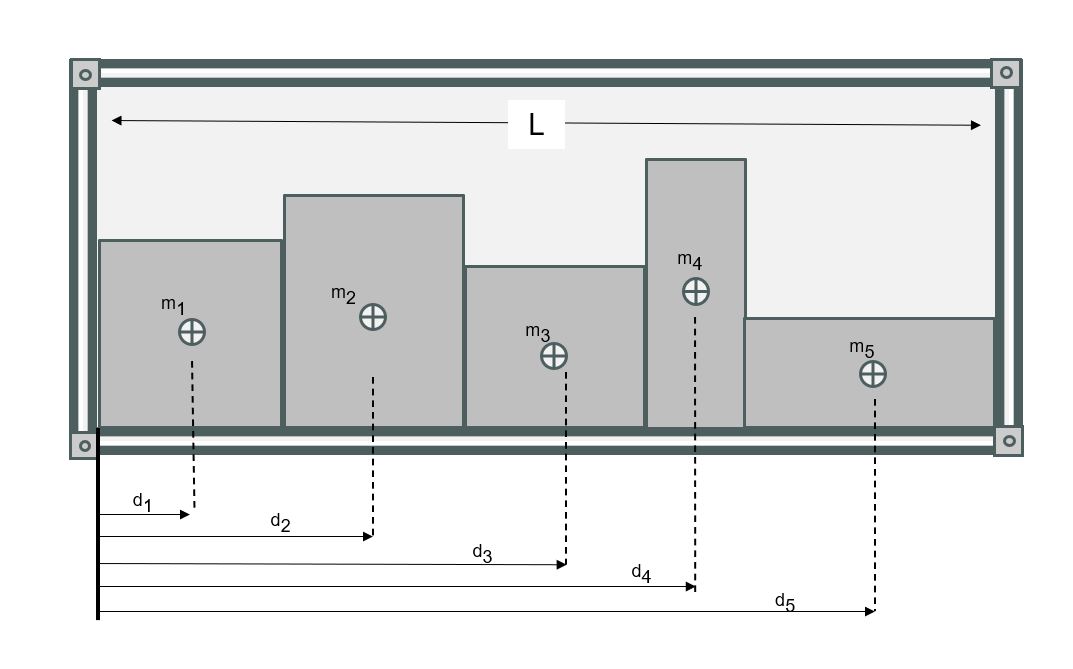
Skizze 1 [CTU-Code Annex 7 Appendix 4]
Conclusion
Correct loading and load securing would have prevented this incident from occurring. The crucial points are:
- Pay attention to the center of gravity: The cargo must be evenly distributed in order to avoid one-sided loads.
- Observe the maximum offset of ±5 %: A shift of weight to one side can cause problems.
- Additional load securing measures: Anti-slip measures and lashing materials prevent the cargo from slipping during transport.
The case looked at here clearly shows that it is not only visible damage that determines transport safety. An eccentric center of gravity can have significant practical repercussions – even causing the transport operation to be suspended. Compliance with the guidelines set out in the CTU Code can prevent such problems and help improve safety during rail transport.
Note:
The most recent officially published version of the CTU Code can be downloaded free of charge via the following link:
https://unece.org/transport/intermodal-transport/imoilounece-code-practice-packing-cargo-transport-units-ctu-codeThis link takes you to the UNECE website. After answering a few anonymous questions, you can download the CTU Code in the following languages:
English (original), Arabic, Chinese, French, Russian, Spanish and German.
Zurück zum Anfang