Photo of the month – April 2007 | [German version] |
Wire entanglement on the highway
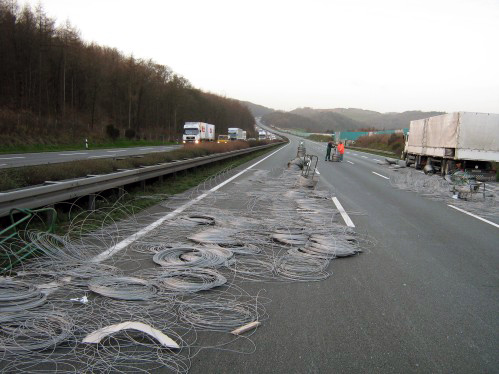
Figure 1 [Grasemann – Jochheim]
This truck/trailer combination was carrying a load of wire coils intended for manufacturing screws. The coils were on loading frames (spools) and loaded with the winding axis facing up. The individual frames were only partially loaded as a tight fit. No load securing measures had been taken. As the truck joined the highway, it was caught by a gust of wind. That driver steered to compensate and the vehicle began to fishtail causing the wire coils on the trailer to break through one of the left side walls and fall onto the carriageway. Large areas of the carriageway were covered by the wire coils, which represented a significant danger to the following traffic.
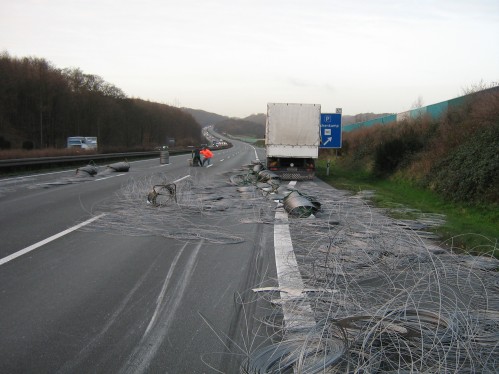
Figure 2 [Grasemann – Jochheim]
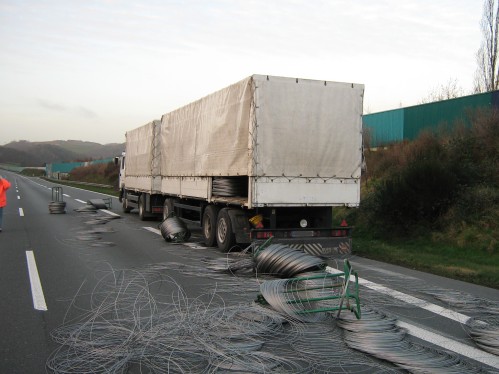
Figure 3 [Grasemann – Jochheim]
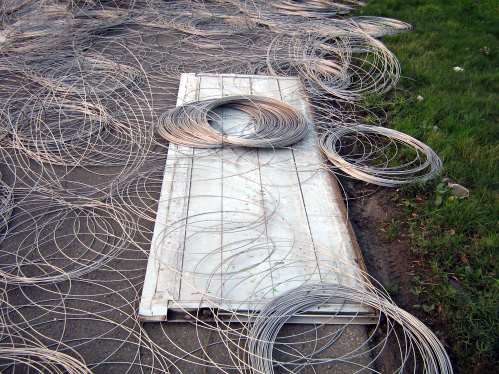
Figure 4 [Grasemann – Jochheim]
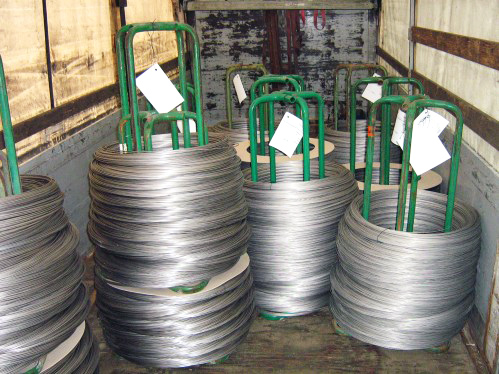
Figure 5 [Grasemann – Jochheim]
Figure 5 shows the wire coils on the truck; some of them are resting relatively loosely on the frames. The coils were loaded offset, in other words, the individual coils were not stowed in rows (soldier stow) but were offset to fill the individual gaps (like the dots on a 5 on a die). A load of this sort has such a high level of flexibility that it is not really possible to speak of a tight-fit load. This means that this load will always have a certain freedom of movement. As far as friction is concerned, the two materials to be assessed are the steel piping frame and the wooden loading area. By no stretch of the imagination can this friction pairing provide a friction of coefficient µ of more than 0.2. It is extremely difficult to judge exactly what happened when the vehicle started fishtailing. The only thing that we can realistically do is to list some of the individual hazards which may have led to this accident.
In the foreground, you can see two stacked spools. It is quite clear that these frames are at risk of tipping. As a result of lateral acceleration, the load on the side wall is considerably higher, as a mass in excess of one tonne can be assumed.
![]() |
It can be assumed that while the vehicle was fishtailing, the brakes were unfortunately applied heavily. Because the load itself was very flexible and it was not loaded as an absolute tight fit, the heavy wire coils were each able to slip forward slightly. As each of the wire coils close up to each other, the force is passed to the front coil until the last coil is supported by the end wall of the trailer or the truck. If the wire coils are loaded offset, it is not only longitudinal force that is generated, but also very considerable lateral force. In combination with the fishtailing and possibly with heavy coils that are in danger of tipping, the side wall has no chance of withstanding the load. |
![]() |
It is common to see that friction-enhancing materials are not even considered for large, heavy loads, as the nonsensical assumption that a heavy load secures itself by its weight alone is still widespread. In fact, the opposite is true. With heavy loads in particular, friction, whose effect is proportional, is of considerable assistance for load securing. Normal anti-slip mats provide a coefficient of friction µ of between 0.5. and 0.6. In the case of frames such as the ones in this example, care must be taken to ensure that the force exerted on the mats does not become too high, otherwise their structure (and hence their coefficient of friction) changes. |
![]() |
When wire coils such as these are loaded, they should not be stacked or alternatively the resulting risk of tipping should be counteracted with special load securing measures such as direct lashing. Since the load itself is flexible and the diameters of the units vary, tight-fit stowage is not possible. Nevertheless, partitioning the loading area can reduce the flexibility to a safe level. A loading area can be partitioned using intermediate walls that form a tight fit with the side walls (i.e. not jammed boards). If this is not possible, as is the case with this vehicle, partitions could be established using three vertical pallets, for instance, connected to each other at the top and bottom by steel rods or squared lumber. In order to ensure that this intermediate wall that is to serve as a loading area partition is able to withstand the forward force from the load, it is secured to the rear with two loop lashings. Well chosen friction-enhancing measures can considerably improve the load securing. The risk of tipping can also be counteracted by attaching loop lashings to three or four of the frames. Any gaps in the load, no matter whether they are at the rear, the side or the front, must either be filled or secured using direct lashings. |
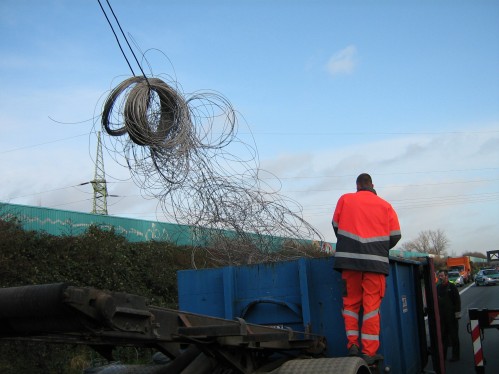
Figure 6 [Grasemann – Jochheim]
Back to beginning