Photo of the month – November 2002 | [German version] |
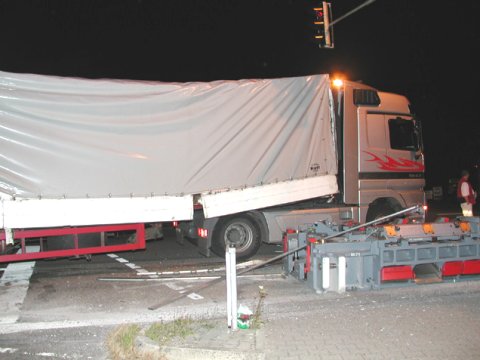
Figure 1
Load securing accident involving a machine part weighing 18.7 metric tons
The articulated truck had to brake hard and swerve to the left in an emergency, causing its load, a press component weighing 18.7 metric tons, to slide to the right on the loading area, smash through the side wall, fall onto the road and come to a standstill behind an automobile. The automobile driver realized what was about to happen and had just moved out of the danger zone by driving forward a little (see Fig. 2).
According to the truck driver, the machine part was resting on 8 hard rubber sheets 20 x 20 cm in size. The vehicle floor consists of perforated pressure plates. Since the rubber sheets are not tested non-slip mats, the material combination steel/hard rubber must be assumed to have a friction coefficient of 0.4. The load was „secured“ with 4 belts (LC (lashing capacity) = 2500 daN) by tie-down lashing without any kind of tight fit.
Calculation of the necessary securing means for this type of securing shows that 38 belts are needed:
![]() |
Required total forwards securing force: 18.7 metric tons x 0.8 g* = 14960 daN | ||||||
![]() |
Frictional securing force: 18.7 metric tons x 0.4 g = 7480 daN | ||||||
![]() |
Lacking securing force: 7480 daN | ||||||
![]() |
Securing force of a tie-down lashing: Prestressing in straight line = 250 daN (0.1 x LC), prestressing in strapping** = 2 x 250 daN = 500 daN *** | ||||||
![]() |
The fact that the belts could not be passed at an angle of 90° from the lashing point to the edge of the load was disregarded for the purposes of this sample calculation. | ||||||
![]() |
Securing action of a tie-down lashing: securing force x friction coefficient = 500 daN x 0.4 = 200 daN | ||||||
![]() |
Number of lashing belts required for tie-down lashing: lacking securing force divided by securing action per belt = 7480 daN / 200 daN = 37.4 –> 38 lashing belts
|
The effort involved in this case could have been reduced considerably by using a different securing method. This machine part could have been entirely adequately secured by two loop lashings on each side, two loop lashings around the front end face and one loop lashing around the rear end face. The belts may have to be protected from sharp edges on the load by suitable means.
Further Figures:
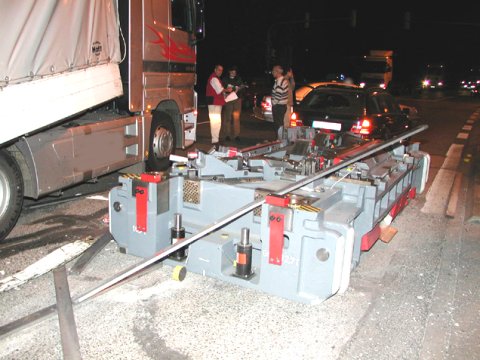
Figure 2
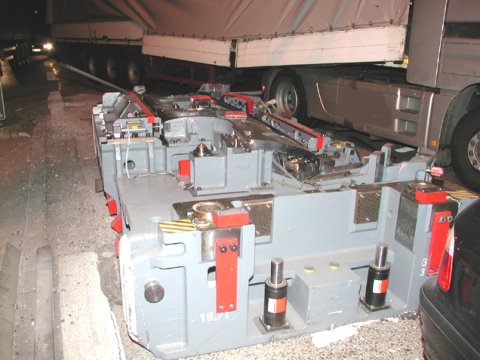
Figure 3
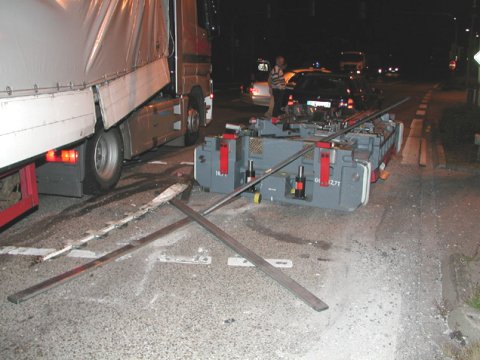
Figure 4
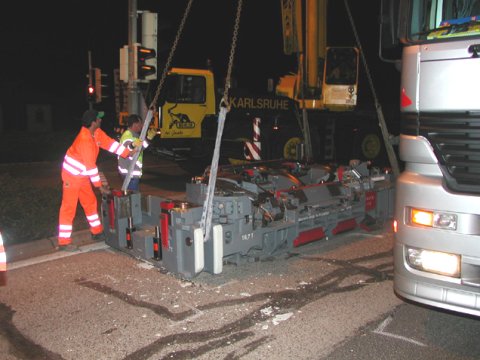
Figure 5
Back to beginning