Foto des Monats – Februar 2014 |
[English version] |
Zick-Zack-Sicherung
Es ist nicht jeden Monat so einfach wie bei diesem Bild des Monats, einen passenden Titel zu finden. Die folgende Abbildung hat es uns sehr leicht gemacht!
Derjenige, der diese Sicherung durchgeführt hat, hat den Gurt mehr oder weniger im Zick-Zack durch die Ladung geführt. Die einzelnen Drahtrollen auf den Kronenstöcken schienen ihm definitiv zu wenig Zusammenhalt zu haben. Ergo, hat er versucht, mit möglichst wenig Druck auf die Ladung und mit wenig Gurteinsatz möglichst viele dieser Ständer miteinander zu verbinden. Augenscheinlich ist es ihm in der Tat gelungen, denn der Gurt steht unter einer gewissen Spannung und stellt irgendwie auch Kräfte zwischen den einzelnen Ständern her.
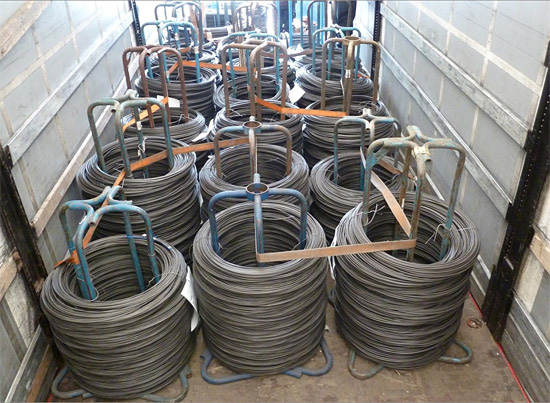
Abbildung 1 [Gerhard Howanietz]
Mit einer Ladungssicherung hat diese Zick-Zack-Sicherung aber herzlich wenig zu tun.
In der Abbildung 2 lässt sich die gesamte Herausforderung dieser Ladungssicherungsanforderung erahnen:
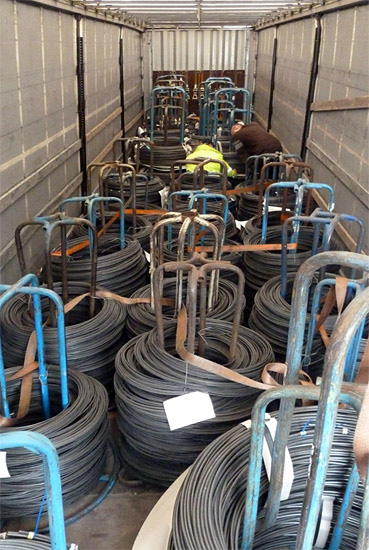
Abbildung 2 [Gerhard Howanietz]
Als Ladungssicherungskolumnisten sind wir recht dankbar für derartige Bilder, denn so viele einzelne Punkte, wie wir diesen Monat besprechen können, finden wir selten auf einmal in einem Bild vereint.
Die vorderen 6 oder 8 Haspeln stehen nicht formschlüssig gegen die Stirnwand. Sie sind etwas größer als die weiter hinten geladenen und weisen zum hinteren Ladungs-„Block“ eine erhebliche Ladelücke auf. In dieser Ladelücke befinden sich gerade der Fahrer und der kontrollierende Polizist, die Einzelheiten der Ladungssicherung hier am Objekt selbst besprechen. Die Aufteilung der Ladung wurde mit an Sicherheit grenzender Wahrscheinlichkeit aufgrund des Lastverteilungsplans so vorgenommen. Grundsätzlich ist es positiv zu bewerten, wenn sich die für die Ladung Verantwortlichen Gedanken zur Lastverteilung machen. Bei diesen Kronenstöcken gibt es gleich mehrere Herausforderungen:
- Sie weisen keine gleichmäßige Geometrie auf. Manche sind an der Basis rund und andere haben eher eine quadratische Form, deren Seiten eingedrückt sind.
- Haben die Kronenstöcke unterschiedliche Größen. Im vorderen Bereich passen nur zwei nebeneinander, im hinteren Bereich drei.
- Lässt sich im oberen Bereich kein Formschluss untereinander herstellen. Wenn Formschluss hergestellt werden kann, dann berühren sich sehr häufig schon die Drahtspulen untereinander oder die Kronenständer in ihrem Basisbereich stehen auf Kontakt zum Nachbarständer. Ein schlüssiger Verbund lässt sich damit aber nicht herstellen.
- Aufgrund der unterschiedlichen Menge an Ladung, die auf die Haspeln gewickelt wurde, haben die Ladeeinheiten kein Modulmaß mehr. D. h., sie passen nicht mehr so auf das Fahrzeug, dass sie zu zweit nebeneinander die Fahrzeugbreite formschlüssig ausfüllen. Somit ist die Nutzung des seitlichen Formschlusses nicht möglich.
In der Abbildung 3 sieht man die Ladelücke zwischen vorderem und hinterem Ladungsblock. Die letzten zwei Kronenstöcke des vorderen Ladungsblockes sind eigentlich vier, denn hier wurden Kronenständer gestapelt. Das Papier, die Kartonage oder der Kunststoff, der zwischen die einzelnen Ständer gelegt wurde, weist darauf hin, dass es sich bei der Ladung durchaus um sensible Ladung handelt:
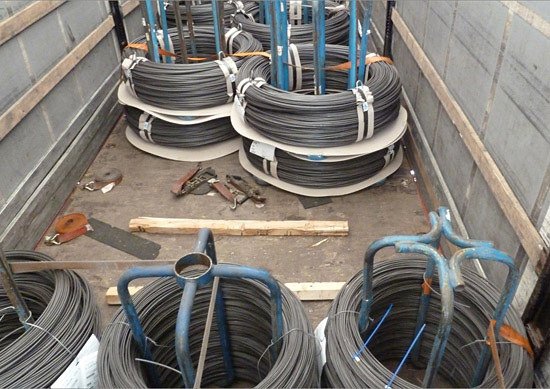
Abbildung 3 [Gerhard Howanietz]
Bevor wir auf weitere Ladungssicherungsdetails eingehen, wollen wir uns den Ladeeinheiten zuwenden. Diese Ladeeinheiten bringen eine ganze Flut von Problemen mit sich. Weder im Basisbereich der Ladeeinheit noch im Kopfbereich lässt sich für die Ladungssicherung ein brauchbarer Formschluss herstellen. Wir brauchen zwar über die Tatsache, dass die Zick-Zack-Sicherung keine ladungssichernde Wirkung entfalten kann, kein weiteres Wort mehr verlieren, aber sie zeigt sehr wohl die Ratlosigkeit desjenigen, der hier eine Ladungssicherung versucht hat. Wahrscheinlich darf er die empfindlichen Drähte nicht einfach niederzurren. Wahrscheinlich ist auch, dass sich diese Drähte kaum sinnvoll niederzurren lassen, weil sie sich nach den ersten paar hundert Metern des Fahrtweges und der Vibration „setzen“ und jegliche Vorspannung aus dem Gurt entweicht. Die Kronenständer selbst sind auch im Kopfbereich so rund, dass jeglicher Versuch, die Ladeeinheit über die Kronenstöcke selbst niederzuzurren, kläglich scheitern würde.
Wie würden sich derartige Ladeeinheiten verbessern lassen?
Offensichtlich werden diese Kronenstöcke sehr häufig verwendet, somit würde sich ein wenig Aufwand ggf. lohnen. Das Zauberwort ist noch einmal die Modulgerechtigkeit. Die Modulgerechtigkeit drückt aus, dass die Ladeeinheit selbst oder ein Vielfaches der Ladeeinheit sich formschlüssig von Seite zu Seite und/oder von vorne nach hinten auf einem Lkw stauen lassen. Das hat den großen Vorteil, dass tatsächlich der Formschluss zur Seite und ggf. nach vorne gut genutzt werden kann, sofern sich denn dieser anbietet. Für diese Ständer würde es bedeuten, dass die Basis der Kronenstöcke ggf. auf einem Metallgestell befestigt würde, welches einer Palette gleich käme. Diese Paletten müssten so bemessen sein, dass entweder zwei von diesen Paletten die Ladebreite eines Fahrzeugs formschlüssig ausfüllen oder drei nebeneinander die Ladebreite eines Fahrzeugs formschlüssig ausfüllen können. Durch diesen Kunstgriff würde sich im Bereich der Basis der Haspeln ein sehr guter Formschluss herstellen lassen. Würden jetzt noch die Kronenstock-„Köpfe“ so gestaltet, dass auf ihnen, möglichst in zwei Richtungen, ein Ladungssicherungsgurt sich sicher auflegen und führen ließe, könnte man diese Haspeln problemlos niederzurren. Das gilt aber nur für den beladenen Zustand, da sich die Haspeln sonst durch die Niederzurrung zueinander neigen würden. Auch wenn drei Kronenständer nebeneinander stünden, könnte man bei formschlüssiger Verladung nach vorne sehr wohl durch eine einzige Niederzurrung drei Kronenstock-Ladeeinheiten problemlos und wirkungsvoll niederzurren. Selbstverständlich setzen wir vernünftiges RH-Material bei dieser Ladungssicherungsart voraus. Mit dem RH-Material wird ein Reibbeiwert von µ=0,6 erreicht. Um auf µ=0,8 zu kommen, müssen also noch 0,2 x die Gewichtskraft der Ladung aufgebracht werden, was durch eine Niederzurrung erreicht wird.
Diese Variante der Niederzurrung (Skizze 1) setzt voraus, dass die Haspeln fest mit den Paletten verbunden sind (z. B. verbolzt) und dass die Drähte unempfindlich gegen Druck sind, da der Gurt seitlich über die Drahtrollen geführt wird:
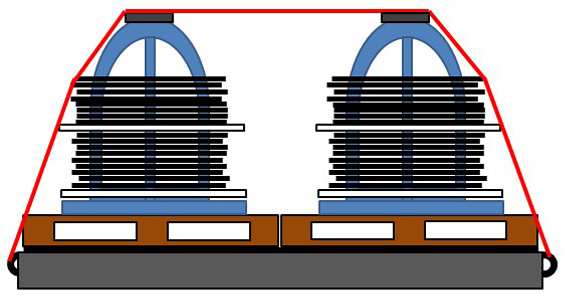
Skizze 1 [GDV]
Sind die Drähte druckempfindlich, kann z. B. eine entsprechend breite U-förmige Schiene über die Kronenstockköpfe gelegt werden, durch die der Gurt geführt wird. Die Schiene sollte passende Ausparungen über den Kronenstockköpfen aufweisen, damit sie nicht verrutschen kann:

Skizze 2 [GDV]
Die Abbildung 4 zeigt sehr schön das Formschlussproblem der Ladeeinheiten. Keine der abgebildeten Ladeeinheiten nutzt nur annähernd den Formschluss, den sie zu einer belastbaren Ladeflächenbegrenzung gewinnbringend nutzen könnte. Die leicht unterschiedliche Form der Ladeeinheiten macht dies nahezu unmöglich:
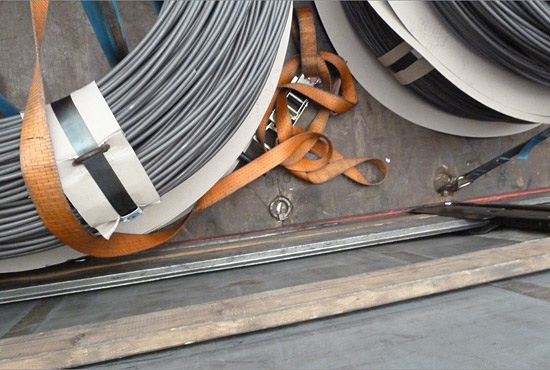
Abbildung 4 [Gerhard Howanietz]
In der Abbildung 5 ist eine sehr lose gefallene Niederzurrung zu sehen. Diese Ladeeinheit besteht aus zwei gestapelten Kronenständern, auf der zumindest auf dem oberen Teil die Drahtrollen relativ fest mit Stahlband zusammengehalten werden. Offensichtlich war es entweder der Flexibilität der Ladung selbst oder der uneinheitlichen Geometrie der Ladeeinheiten geschuldet, dass diese Niederzurrung vollkommen unwirksam geworden ist:
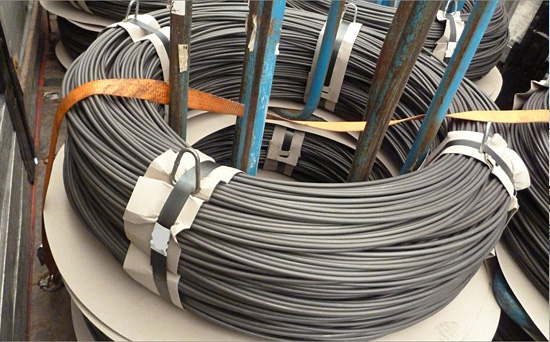
Abbildung 5 [Gerhard Howanietz]
In der Abbildung 6 sehen wir die ersten beiden Ladeeinheiten, die nicht gegen die Stirnwand gestaut wurden. Sie sind wiederum gestapelt, bestehen aus großen Kronenständern und es wurde der Versuch einer Niederzurrung unternommen:
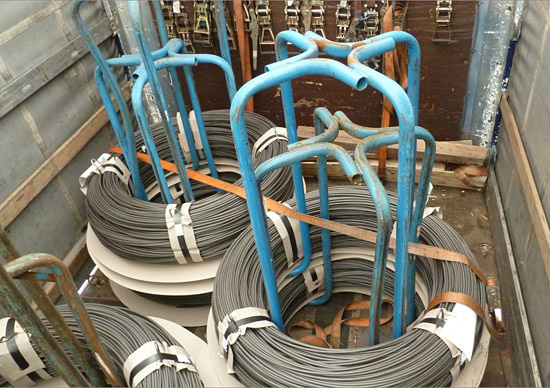
Abbildung 6 [Gerhard Howanietz]
Mit etwas gutem Willen könnte man bei dieser Niederzurrung auch von einer gewissen Wirkung ausgehen. Obwohl bei der rechten Ladeeinheit zu vermuten ist, dass der Gurt die Ladeeinheit schon ein wenig nach vorn drückt, aber wir wollen ja nicht päpstlicher sein als der Papst. Mit Interesse nehmen wir an diesem Bild wahr, dass allein an der Stirnwand 15 oder 16 Spannelemente hängen. Teils mit kurzen, teils mit längeren Spannhebeln. Dieses Fahrzeug scheint also exzellent mit Ladungssicherungsmaterial ausgerüstet zu sein. Hinweisen möchten wir auch schon bei diesem Bild, dass versucht wurde, unter die Ladeeinheiten zumindest partiell RH-Mappen unterzulegen.
In den Abbildungen 7, 8 und 9 wenden wir uns intensiv dem Ladeboden zu. Auf der Abbildung 7 ist eindeutig zu erkennen, dass es sich hier um einen Ladeboden handelt, der schon reichlich Gebrauchspuren aufweist:
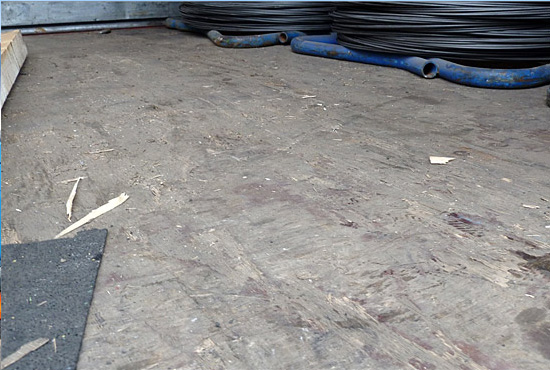
Abbildung 7 [Gerhard Howanietz]
Es ist davon auszugehen, dass dieser Ladeboden keine vollkommene ebene Fläche mehr darstellt, vielmehr wird er Höhenunterschiede in mehreren Millimetern Stärke aufweisen. Dazu sieht man auf dieser Abbildung, dass die Ladeeinheiten auf dem blanken Ladeboden stehen, ohne jegliche RH-Matte. Darüber hinaus ist zu sehen, mit welcher Qualität von RH-Matten das Fahrzeug ausgestattet ist. Vom Zustand der RH-Matten wollen wir später sprechen. Ein wichtiges Faktum ist aber, dass diese auf Abbildung 7 zu sehende RH-Matte eine maximale Stärke von 2 oder 3 Millimetern hat. Wie sollen derart dünne RH-Matten bei einer so stark abamüsierten Ladefläche die Ladeeinheiten reibungstechnisch wirksam von der Ladefläche trennen? Dies scheint unmöglich.
In der Abbildung 8 setzt sich das Reibungsthema weiter fort. Welche Reibung kann hier angenommen werden? Die Ladeeinheit steht auf einem durch den Gebrauch relativ glatten Stahlträger. Somit kann hier nur ein Reibbeiwert von μ = 0,1 oder μ = 0,2 angenommen werden:
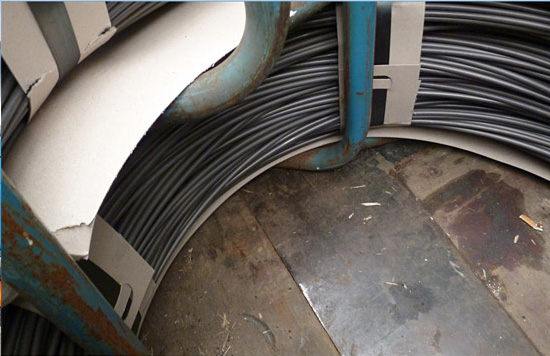
Abbildung 8 [Gerhard Howanietz]
Und in der Abbildung 9 ist das Reibungssammelsurium perfekt. Teilweise steht die Ladeeinheit auf einem Stahlträger, teilweise auf der Ladefläche und vielleicht auch ein kleines bisschen auf der viel zu dünnen RH-Matte. In diesem Fall haben die RH-Matten noch nicht einmal Alibifunktion. Es scheint so, als ob sie eher zufällig auf der Ladefläche herumliegen und die Ladeeinheiten in Bezug auf die RH-Matten wahllos auf der Ladefläche abgestellt wurden:
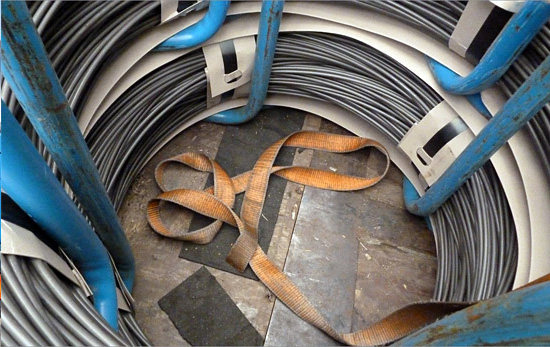
Abbildung 9 [Gerhard Howanietz]
In der Abbildung 10 fällt dem geneigten Leser auf, was ihn wahrscheinlich schon während der letzten drei Bilder mehr oder weniger geärgert hat. Die Ladefläche ist alles andere als sauber. Sie ist sogar derart verschmutzt, dass auch die RH-Matte nicht frei davon ist. Die RH-Matte weist intensive Gebrauchsspuren auf, wie vorab schon erwähnt, eine viel zu geringe Stärke, um die Ladung tatsächlich reibungstechnisch aus der Ladefläche herauszuheben und an all den markierten Stellen wurde diese RH-Matte schon überlastet. Das kann durch andere Ladung passiert sein, aber auch sehr wohl durch die Kronenstock-Gestelle, denn durch die Rohre berührt nur eine linienförmige Fläche die RH-Matte und übt ggf. einen erheblichen Druck aus. Hier wird aus einer RH-Matte leicht eine „Krümelmatte“, d. h., dass sich die Matte in einzelne Krümel auflöst und nun kontraproduktiv wirkt, so als wären die Ladeeinheiten Heinzelmännchen auf den Erbsen:
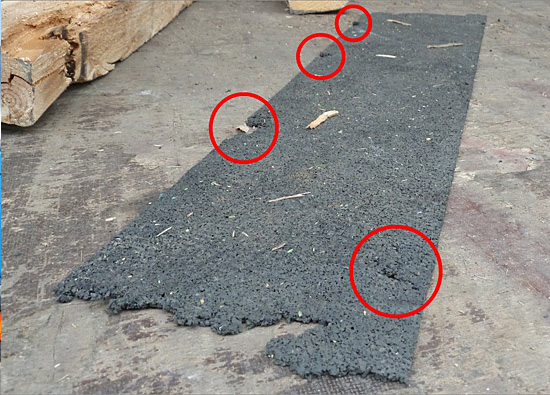
Abbildung 10 [Gerhard Howanietz]
Merke:
Grundsätzlich müssen RH-Materialien die Ladeeinheiten reibungstechnisch aus der Ladefläche herausheben. D. h., sie müssen so stark sein, dass keine Stelle der Ladung die Ladefläche berührt, sondern nur auf RH-Material steht. Zudem ist es bei derart robustem Gebrauch ratsam, Schwerlastmatten von einer Stärke von 8 bis 12 Millimetern zu verwenden. Nur dann lassen sich die überaus positiven Effekte beim Gebrauch des RH-Materials auch erzielen.
In dieser Abbildung sind für uns die Einstecklatten von besonderem Interesse. Die unteren beiden sind aus Aluminium und die obere aus Holz:
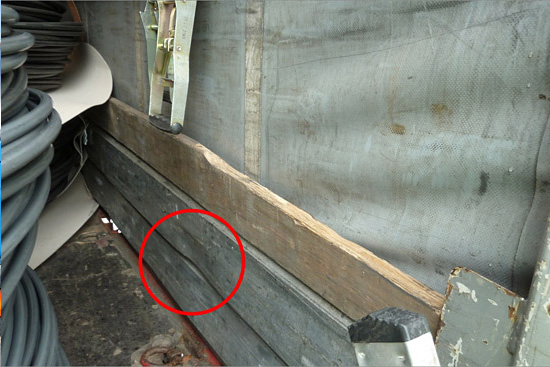
Abbildung 11 [Gerhard Howanietz]
Mit diesen Einstecklatten lässt sich ggf. je nach Qualität und Ausführung eine belastungsfähige Ladeflächenbegrenzung herstellen. Voraussetzung dafür ist, dass sich die untere Aluminium-Einstecklatte mit ihrer Profilierung im Fahrzeugrahmen oder auf der Ladefläche formschlüssig abstützen kann. Dieser Formschluss muss von Aluminiumlatte zu Aluminiumlatte weitergegeben werden. Der markierte Bereich zeigt eine Aluminiumlatte, die eingebeult ist. Derartige Einbeulungen passieren immer dann, wenn das Fahrzeug abgeplant ist und die Aluminiumlatten nicht weit genug unter das Fahrzeug geschoben wurden, sodass der Gabelstapler darauf oder darüber fahren kann. Da die Breite dieser Einstecklatten eine maßgebliche Größe ihrer Festigkeit sind, heißt dies im Umkehrschluss, wenn diese Einstecklatten plattgefahren wurden, haben sie auch keine Wirkung mehr. Die Holzlatte, die oben aufliegt, ist am Ende schon weit ausgebrochen, dass sie besser nur noch als Feuerholz dient. Eine belastungsfähige Ladeflächenbegrenzung wie mit Aluminium-Einstecklatten, die entsprechend profiliert sind, kann man mit derartigen Holzlatten sowieso nicht herstellen.
Hinweis:
Im vorliegenden Fall ist nicht zu einem Unfall gekommen. Vielleicht war es Glück für den Fahrer, dass er von der Polizei angehalten und kontrolliert wurde. So konnte ihm, aber auch dem Halter und dem Verlader erklärt werden, dass diese Ladungssicherung absolut nicht ausreichend gewesen ist.
Oft reicht nur eine Ausweichlenkung und die Ladung fällt von der Ladefläche. Das dies kein konstruierter Gedankengang ist, beweist unser Foto aus dem Monat April 2007. Dort ist die Ladung aud die Autobahn gestürzt.
Allzeit sichere Fahrt wünschen Ihnen Ihre Ladungssicherungskolumnisten – und seien Sie immer auf Draht!
Zurück zum Anfang