Foto des Monats – Mai 2012 |
[English version] |
Auf des Messers Schneide
Für einen Ladungssicherungskolumnist sind Stahlverladungen überaus dankbar. Nicht weil Stahlverladungen besonders schlecht verladen und gesichert werden, aber sie verlangen in der Regel von demjenigen, der die Verladung veranlasst, durchführt und dann die Ladungssicherung vornehmen muss, relativ viel ab. So lassen sich mit einem Bild des Monats wieder viele verschiedene Fehlerchen aufzeigen und auch gleich die richtigen Empfehlungen dazu geben.
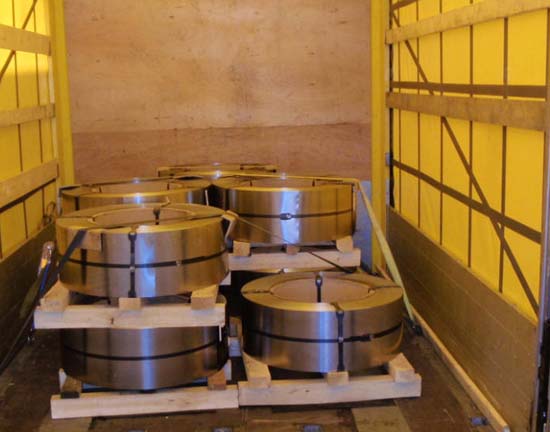
Abbildung 1 [GDV]
Dieses Fahrzeug war mit dieser Vorladung ca. 4,5 Tonnen Spaltbändern aufs Skits bzw. Paletten auf der Straße. Es entzieht sich unserer Kenntnis, wie viele Kilometer dieses Fahrzeug zurückgelegt hat, Fakt ist aber, dass das nächste Unternehmen, welches auf diesem Fahrzeug zuladen sollte, geradezu erschrocken ist, ob der Sorglosigkeit der vorgefundenen Verladung und Sicherung.
Schon die Lastverteilung scheint überaus problematisch. Die Spaltbänder stehen direkt an der Stirnwand. Das hat Vorteile, wenn man den Formschluss sucht und ihn zu nutzen weiß. Stellt man sich aber nun eine Lastverteilungskurve vor, in der ca. 4,5 Tonnen auf den ersten 20 Prozent der Ladefläche stehen, und der Rest der Ladefläche ist vollkommen leer, könnte das schon problematisch werden.
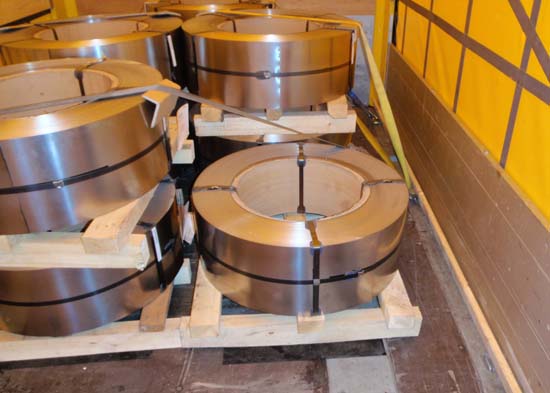
Abbildung 2 [GDV]
Tritt man näher an die Ladung heran, werden die Probleme klarer. Die Bleche sind auf einen Kern, wahrscheinlich aus relativ stabiler Pappe, gewickelt und werden mit Stahlbändern zusammengehalten. So weit so gut. Positiv hervorzuheben ist, dass die Stahlbänder vor den scharfen Kanten der Stahlbleche und umgekehrt geschützt sind. Beim weiteren Herstellen einer Ladeeinheit war man weniger sorgfältig. Wobei weniger sorgfältig ein bisschen untertrieben ist. Die Ladung liegt einfach auf sogenannten Skits. Das sind drei Vierkanthölzer, auf die drei bohlenformatige Hölzer derart genagelt sind, dass auf ihnen diese Spaltbänder gelagert werden können. Im vorliegenden Beispiel sind die Spaltbänder derart auf die Skits positioniert bzw. die Skits so dimensioniert worden, dass eine wirkungsvolle formschlüssige Verladung nur schwer, teilweise oder gar nicht herzustellen war.
Unter den Skits finden wir reibungserhöhende Matten, das ist grundsätzlich positiv, aber die Art und Weise, wie sie untergelegt wurden, lässt Wünsche offen. Erfährt das Fahrzeug eine seitliche Beschleunigung, kann sich der Skit zur Seite lehnen (insbesondere, wenn die Ladung gestapelt ist) und der Skit bekommt direkten Kontakt zur Ladefläche. In diesem Moment kann die gute Reibung des Gummis nicht mehr voll umfänglich wirken und es ist nicht mehr sichergestellt, dass nur noch die gute Reibung der RH-Materialien wirkt. Somit kann bei der Berechnung der Ladungssicherung auch nicht mehr mit den hohen Reibbeiwerten gerechnet werden.
Wie ist diesem Umstand abzuhelfen? Am besten man legt unter alle vier Ecken RH-Materialien mit einer Stärke von 8-10 mm unter, um die Skits reibungstechnisch vollkommen von der Ladefläche zu trennen. Dabei ist es sinnvoll, wenn die RH-Matten ein wenig über die Hölzer hinausragen, damit zu jeder Zeit die vollkommene reibungstechnische Trennung der Skits von der Ladefläche gewährleistet ist. Sollten die Skits durch das hohe Gewicht der Ladung in der Mitte „durchhängen“, so dass die Gefahr besteht, dass die Kufenhölzer Kontakt zur Ladefläche bekommen, ist es sinnvoll, auch in der Mitte noch RH-Materialien unterzulegen.
So gut das Erhöhen des RH-Wertes grundsätzlich ist, in diesem Beispielfall wurde nur sehr halbherzig gehandelt. Die Ladung selbst steht Stahl auf Holz (Skit), die zweite Lage dieser Spaltbänder steht erneut Stahl auf Holz. Im Falle einer Beschleunigung würde die Ladung von dem Skit rutschen, dieses würde aber auf Grund der guten Reibung an Ort und Stelle liegen bleiben. Der Effekt für die Ladungssicherung durch das Gummi ist Null.
Wie kann man diesen Umstand verbessern?
Entweder werden die Stahlbänder auf den Skits mit Stahlband an allen vier Seiten mit eingebunden oder die Spaltbänder werden auf den Skits mit Unterlagen aus RH-Material gelegt. Auch die Ladung in der 2. Lage muss konsequent auf RH-Materialien gelagert werden, damit die „Reibungskette“ nicht abreißt. Nur so wäre eine Reibung zu erreichen, die die Ladungssicherung deutlich erleichtert. Wie auf den Bildern andeutungsweise zu sehen, würde eine geschlossene Reibungskette den Versuch der Ladungssicherung mittels Niederzurrungen rechtfertigen.
Beim linken oberen Stahlband sieht man schon, wie sich der Kantenschutz vom Spaltband löst und der Gurt Gefahr läuft, sein Leben auf den messerscharfen Kanten der Spaltbänder auszuhauchen. Beim rechten unteren Spaltband läuft der Ladungssicherungsgurt im Vordergrund gleich über die scharfe Kante des Spaltbandes mit dem Erfolg, dass er spätestens nach diesem Einsatz ablegereif ist oder im Falle einer Beschleunigung, das heißt einem Verrutschen des Spaltbandes, sofort durchtrennt wird.
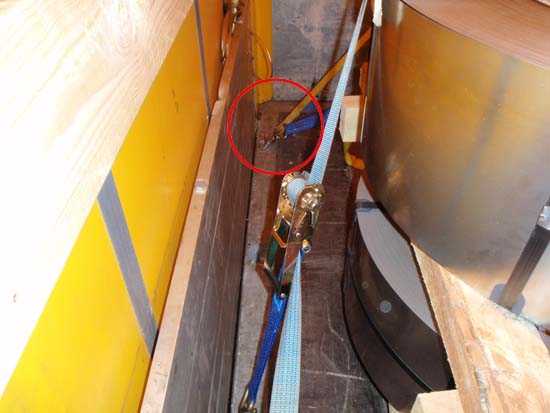
Abbildung 3 [GDV]
Schön zu sehen ist auf dieser Abbildung, dass das obere Spaltband einfach so auf dem Skit liegt. Weder ist es mit den Stahlbändern, die zur Verpackung der Spaltbänder dienen, mit eingebunden, noch liegen irgendwo RH-Materialen unter der Ladung. Zu sehen ist auch, dass das obere Stahlband entweder beim Transport mit den Flurförderzeugen, bei der Verladung oder beim Transport mit dem LKW schon auf dem Skit verrutscht ist. Dass eine Ladungssicherungsmaßnahme, die aus Niederzurrungen besteht, bei derartiger Verladung und Ladeeinheitenbildung nicht sonderlich sinnvoll und in keiner Weise wirkungsvoll ist, muss an dieser Stelle sicher nicht weiter erwähnt werden.
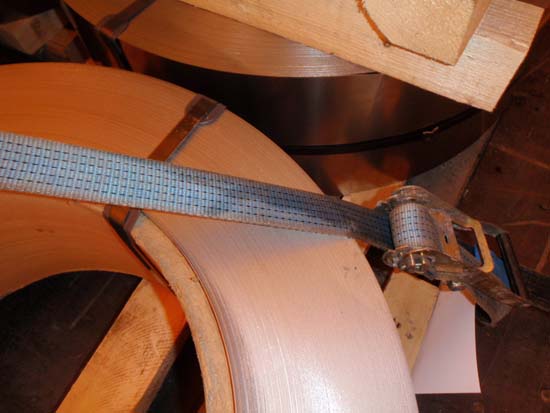
Abbildung 4 [GDV]
Die Abbildung 4 zeigt das vorhin angesprochene rechte untere Coil mit dem Gurt im Vordergrund. Die „Schnittstelle“ ist klar zu erkennen und lässt den geneigten Leser dieser Kolumne sicherlich nur mit Kopfschütteln ergrausen.
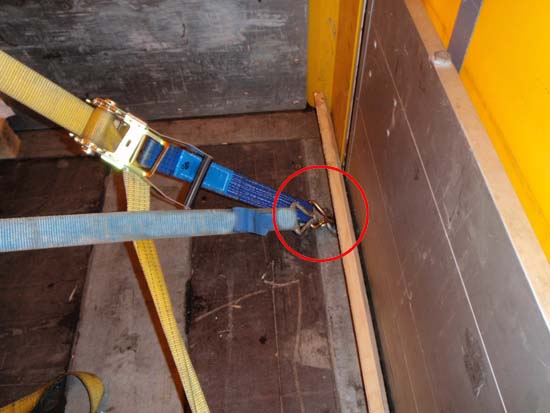
Abbildung 5 [GDV]
Nicht genug, dass die Ladungssicherungs- und Verpackungsmaßnahmen nicht gerade vorbildlich sind, nein, man war auch im Detail noch recht „erfinderisch“. Auf der Abbildung 5 ist zu sehen, dass der Gurt in sich selbst eingehakt wurde. Da kein geeigneter Ladungssicherungspunkt an der richtigen Stelle mehr zur Verfügung stand, wurde der Haken des Spannelementes als Ladungssicherungspunkt verwandt. Auch wenn sich ein derartiges Vorgehen anzubieten scheint, ist es in keiner Weise sinnvoll, da die Haken für eine derartige Belastung nicht geeignet sind.
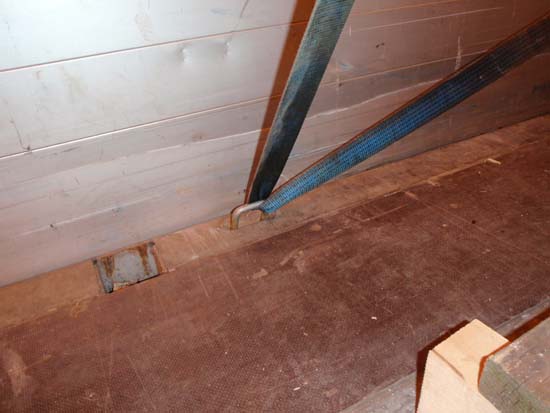
Abbildung 6 [GDV]
Auf dieser Abbildung ist der gleiche Gurt zu sehen wie auf der Abbildung 5, nur auf der anderen Fahrzeugseite. Positiv hervorzuheben bleibt hier nur, dass derjenige, der die Ladungssicherung durchgeführt hat, wohl intuitiv gefühlt hat, dass diese Ladungssicherung, die er hier gerade in die Tat umsetzt, wohl unzureichend ist und er sich irgendwie ein wenig weiter auf die sichere Seite begeben wollte. So leicht und gut Gurte im Allgemeinen zu handhaben sind, eine Einschnürung -wie in diesem Beispiel- bei der Durchführung des Gurtes durch den Ladungssicherungspunkt vertragen sie nicht, denn sie werden dadurch in ihrer Halte- und Sicherungskraft reduziert.
Wie wird eine derartige Ladung richtig verpackt und gesichert?
Eine Variante ist es, die Spaltbänder mit Stahlband auf den Skits zu befestigen, sodass sie eine Ladeeinheit bilden. Auch hierbei muss man Sorgfalt walten lassen. Z. B. müssen die Bänder, die unter den Kufenhölzern liegen, in einer Nut laufen, sodass sie beim Aufnehmen, Transport und Absetzen der Ladeeinheit mittels Flurförderzeug (z.B. Gabelstapler) vor Beschädigung geschützt sind. Die Skits sollten größentechnisch auf die Spaltbänder abgestimmt sein und zwar so, dass sich weder ein Überstand noch ein Rücksprung ergibt. D. h. die Spaltbänder stehen nicht über das Skit hinaus, stehen aber auch nicht vom Rand des Skits zurück und ermöglichen so eine formschlüssige Verladung Skit an Skit und Spaltband an Spaltband. Nur so kann sich die Ladung aneinander abstützen und auch tatsächlich über den erlangten Formschluss sichern. Darf sich die Ladung, aus welchem Grunde auch immer, nicht direkt aneinander abstützen, muss noch mehr Aufwand bei der Verbindung zwischen Skit und Spaltband mittels Stahlband getrieben werden, sofern die Ladung über den Formschluss der Skits gesichert werden soll.
Werden die Spaltbänder nicht mittels Stahlband an den Skits befestigt (mit eingebunden), so gibt es die Möglichkeit, die Spaltbänder mittels RH-Material (welches aber durchvulkanisiert sein sollte, damit es nicht so schnell zerschnitten wird) auf den Skits zu verladen. Gestapelte Skits müssen selbstverständlich auch mit RH-Material unterlegt werden. Auch dieses RH-Material sollte durchvulkanisiert sein. Bei einer derart guten Reibung kann jetzt niedergezurrt oder durch die Coilaugen eine Direktsicherung mittels Umspannung vorgenommen werden.
Peinlich genau ist darauf zu achten, dass der Kantenschutz derart angebracht ist, dass er auf gar keinen Fall abrutschen kann. Schutzschläuche über Gurte ggf. mit zusätzlichen Kantenschutzmaterialen sind dringend zu empfehlen.
Gez. die Ladungssicherungskolumisten
Zurück zum Anfang